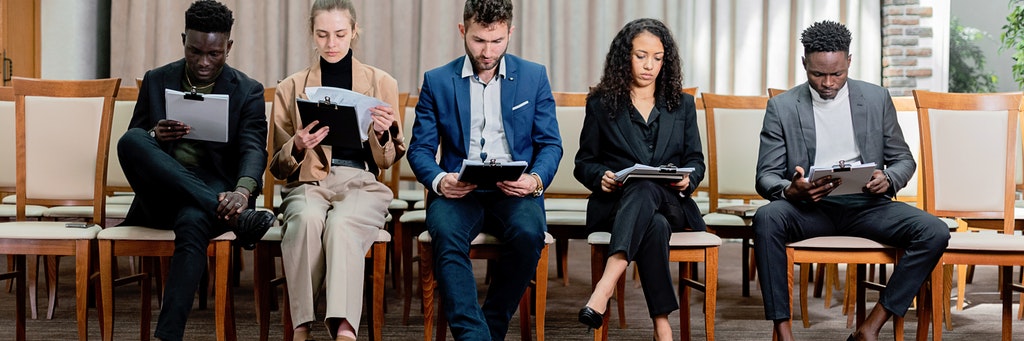
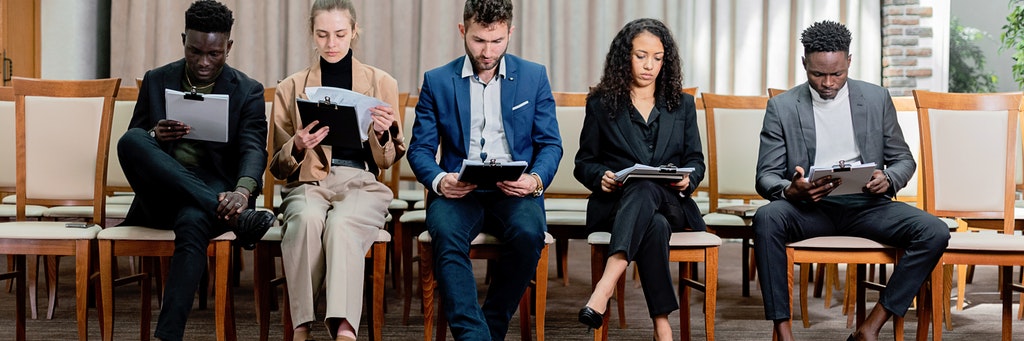
Guide to Establishing and Running a Project Safety Committee (PSC)
Our Second Safety Management Procedure is the Project Safety Committee. Okay, so committees are not the sexiest subject, but we need to get stakeholders together to make things happen!
Project Safety Committee: Introduction
In safety-critical industries such as defense, aerospace, and engineering, maintaining a robust safety management system (SMS) is paramount. A Project Safety Committee (PSC) plays a vital role in overseeing, coordinating, and ensuring safety compliance throughout the lifecycle of equipment and systems. This guide will explore the role, objectives, and procedures of a PSC, as defined in UK Def Stan 00-56, and provide insights on how to structure and run a PSC effectively.
What is a Project Safety Committee (PSC)?
A Safety Committee is defined as:
A group of stakeholders that exercises, oversees, reviews and endorses safety management and safety engineering activities.Def Stan 00-56
Simply put, the PSC is a formal body composed of experts and decision-makers from various disciplines, convened to ensure that safety-related decisions are well-founded, thoroughly vetted, and correctly implemented.
Objectives of a PSC
The key objectives of a PSC are to ensure effective coordination, agreement, and proper response from those with safety responsibilities. Specifically, the PSC achieves the following:
- Coordination of Safety Issues: The PSC acts as a platform where all stakeholders responsible for safety management can ensure coordination on safety issues, eliminating silos.
- Access to Knowledge: It provides decision-makers with access to relevant knowledge and expertise across different domains, including engineering, maintenance, user experience, and risk management.
- Oversight of the Safety Case: The PSC ensures competent oversight of the safety case throughout its development and maintenance.
- Audit Trail: keep detailed meeting records, and establish an audit trail showing that advice was sought and safety decisions were grounded in expertise.
The PSC should facilitate smaller working groups or sub-committees to address specific safety issues when necessary, ensuring that no aspect of the safety management process is overlooked.
In Australia, it is a legal requirement for those with safety responsibilities (Duty Holders) to consult, coordinate and cooperate with others. Other countries may use different terms for similar requirements. The bottom line is that it's a good idea!Top Tip
Project Safety Committee: Procedure
Membership of the PSC
The effectiveness of a PSC largely depends on its membership, which should include representatives with specific roles and expertise, as appropriate to the project. Typical members might include:
- Delivery Team Representatives (e.g., Project Safety Manager)
- Logistics Support Teams
- Equipment Support Teams
- Customer and User Representatives
- Prime Contractors and Subcontractors
- Design Organization
- Independent Safety Auditor
- Specialist Advisors
- Regulator / Safety Authority
- Safety and Environmental Protection Group
Moreover, it may also include contractors, consultants, and subject matter experts from other government departments or foreign defense bodies.
However, don't invite anybody and everybody 'just in case', as this devalues the PSC and its work. Top Tip
More information on PSC membership has been provided in Annex A - example Terms of Reference for a PSC.
Chair and Quorum
A critical element of any PSC is competent leadership. The PSC Chair must be a safety-competent individual holding formally-delegated authority for the program's safety tasks, typically defined in a Letter of Delegation. This document outlines the chairperson’s responsibilities and authority.
For a PSC to conduct its business, it must be quorate, meaning a minimum number of key members must be present. This quorum usually consists of:
- Delivery Team safety delegation holder
- Project Safety Manager
- Design organization representative
- Customer representative
- Safety Case author
If a quorum is not achieved, the meeting can still proceed, but decisions will only be implemented after receiving approval from the absent quorum members..
Quorum
In order for a PSC to make decisions concerning the safety of a capability or equipment, it should be declared quorate at the beginning of the meeting. In order for a PSC to be declared quorate, the following SQEP and authorized members should be in attendance:
- Delivery Team safety delegation holder
- Project Safety Manager
- Design organization
- Customer representative (Project Sponsor)
- Safety Case author
The quorate for a PSC can be expanded depending on the nature of the project. Details should be provided in the Project Safety Management Plan (SMP) or Terms of Reference.
If a quorum is not achieved, the meeting can still proceed, but decisions will only be implemented after receiving approval from the absent quorum members.
This is a good point. PSCs don't always meet frequently, and getting some members to attend can be challenging. Nevertheless, it is important to keep moving forwards.Top Tip
Meeting Frequency and Structure
PSC meetings should be scheduled regularly, though the frequency will depend on the project’s complexity and phase. Typically, meetings occur more frequently during the early design and review stages, and less frequently once the system is in service.
For smaller projects, PSC activities can be integrated into broader project meetings, ensuring safety remains a specific agenda item. Larger or more complex projects may require dedicated PSC meetings with support from Working Groups to assess hazards or system integrity.
Working Level Support
Depending on the complexity of the project, one or more working groups may be established that support the PSC by assessing hazards or reviewing the integrity of specific systems. Integrity working groups could consider structure, propulsion or other electrical or mechanical systems, reporting significant issues to the PSC.
Role of the Safety Management Committee (SMC)
For large-scale projects or portfolios, a Safety Management Committee (SMC) may be established to manage multiple PSCs across similar systems. This ensures consistency in safety management policy and strategy across projects. The SMC will oversee the activities of individual PSCs, ensuring adherence to safety management plans (SMPs).
Figure 2.1 shows an example of a Safety Committee structure, together with the management documents that sit at the relevant committee level.
Figure 2.1 - Safety Committee Structure
Safety Committee Structure
Figure 2.1 represents an example of a Safety Committee structure, with supporting working groups and hazard reviews in place. Teams can modify the structure of the Safety Committees to suit the specific organization of the program. The emphasis should be on establishing a Safety Committee with suitable chairmanship and Terms of Reference.
The structure shown in Figure 2.1 would be suitable for a large Program managing several important projects. However, it is probably overkill for most projects. With committees, less is sometimes more.Top Tip
Project Safety Committee Authority and Competence
The chairman of the PSC should hold a Letter of Delegation detailing the authority for carrying out the safety management tasks on that program.
The PSC exists to provide information and specialist advice to those who have specific responsibility for safety management on an acquisition project so that they can reach informed decisions. The Project safety delegation holder should seek and consider relevant advice through the PSC but remain the decision-maker.
While not all members of the PSC need to have specific competence and experience in Safety Management, some committee members must have this competence and are consulted. In addition to the safety delegation holder, whose competence must be established before their delegation being issued, other members of the PSC who must be safety competent would typically include the Project Safety Manager and the Independent Safety Auditor (if appointed).
As a minimum, the Project Safety Manager should have system safety competence at the practitioner level. Competence requirements for the safety delegation holder will be defined in a relevant Assignment Specification.
The level of competence needed is driven by many factors - size, complexity, novelty - and this will be discussed under a post on 'Proportionality' (TBD). Top Tip
Where beneficial, combine committees for safety and environmental management activities. Align programs as far as possible and share data where relevant.
Where there are separate safety and environmental committees, these could meet consecutively over the morning and afternoon. Members and specialists should attend as appropriate to each.
The PSC covers groups of similar projects within a Delivery Team where common activities are required. Separate committees are better for very large, high risk or diverse projects within a Delivery Team.
The PSC meets regularly as a body, or its work is included as a permanent item in another forum (in this instance care should be taken that all relevant parties are included), or simply through written communications. This last option is less desirable because there is no opportunity for direct interaction.
Record-Keeping and Documentation
Accurate record-keeping is vital to ensure transparency, accountability, and auditability. PSC meeting minutes should document:
- Attendees
- Key discussions
- Advice and recommendations
- Decisions made
- Agreed actions
These records often feed into larger project documentation, such as the System Requirements Document, Through Life Management Plan, and Safety Management System (SMS).
Review and Agreement of Safety Documents
A key PSC function is reviewing safety documents and advising the safety delegation holder on their suitability. Agreement can be recorded formally via document sign-offs or recommendations in PSC minutes. This process ensures that all safety documentation, including the Safety Case, meets the required standards before formal approval and implementation.
Risks and Pitfalls
Failure to establish or effectively run a PSC can lead to significant risks for a project, including:
- Incomplete stakeholder engagement, leading to safety requirements not being adequately defined.
- Inappropriate safety activities, if the PSC does not review and approve the SMP.
- Infrequent meetings, potentially delaying issue identification, risking project time and cost.
- Lack of clear authority, causing confusion between Enterprise and contractor responsibilities, which could shift accountability from the designers to the PSC.
By mitigating these risks through clear terms of reference, structured meetings, and well-defined roles, the PSC can ensure project safety management remains robust and reliable.
Beware of the PSC delving into detail and doing what is expedient, rather than was is needed. Set appropriate TORs and agendas and stick to them.Tip Top
If the PSC does not meet with sufficient frequency, then they may not identify in a timely manner, any issues with the safety program. This could result in impacts on project time and cost.
If the PSC attempts to control the detailed design solutions, rather than relying on the contractor’s Safety Committee and design function, then Enterprise will take responsibility from the designer. Enterprise staff will be represented on the contractor’s Safety Committee and shall exercise influence at that forum and through setting appropriate requirements.
Project Safety Committee: Timing
Formation
Establish the PSC during the Concept phase of a project by the Customer, or Requirements Manager, through the Capability Working Group, in conjunction with the relevant Project Director, to set out the safety requirements for the equipment.
The PSC has an important role to play in influencing safety requirements. This is not mentioned in 'PSC: Required Outputs', below, but is possibly the PSC's most important contribution.Top Tip
Meetings
The required frequency of the PSC meetings depends on various factors including the stage of the project, the complexity of the system, and whether the PSC is supported by Working Groups or has complete responsibility. Hold meetings at greater frequency during periods of significant review and decision-making, typically when project milestones are approaching.
PSC meetings may occur less frequently during periods of stability, such as during the in-service phase, when fewer safety decisions are necessary. However, the PSC still has an important duty to provide oversight of the Safety Case and ensure that it remains valid and monitoring safety performance. Consider whether the system or its usage is changing and seeking counter-evidence that shows the predicted level of safety performance is not being achieved in practice.
Project Safety Committee: Required Inputs
The procedure may use the following reference inputs, as available:
- Outputs from procedure SMP01 – Safety Initiation;
- Documents to be reviewed such as:
- Project Safety Management Plan;
- Independent Safety Auditor Audit Plan (if appointed);
- Independent Safety Auditor Audit Report (if appointed);
- Other Safety Audit Plans (e.g. self or Peer audit);
- Safety Audit Report;
- Hazard Log Report;
- Safety Requirements;
- Safety Assessment Report;
- Safety Case Report.
- Acquisition System Guidance Functional Competencies for System Safety Management;
- Records of previous meetings of the Safety Committee.
Project Safety Committee: Required Outputs
The outputs of the procedure will comprise:
- Established Safety Committee membership;
- Defined Terms of Reference for the Safety Committee (see Further Guidance – Examples Terms of Reference for Project Safety Committee);
- Records of Safety Committee meetings, including advice given and the actions, agreed;
- The advice given by members of the Safety Committee should include recommendations on whether a reviewed document (e.g. Safety Management Plan or Safety Case Report) should be authorized by the Project Director. If authorization is not recommended, then the reasons should be recorded.
Conclusion
The establishment and management of a Project Safety Committee (PSC) are critical to the safe delivery of defense and engineering projects. Through clear objectives, expert membership, and rigorous oversight, the PSC ensures that safety remains at the forefront of project decision-making, thereby protecting both people and assets.
By following this comprehensive guide, organizations can structure their PSCs effectively, aligning with safety standards and regulatory requirements. The PSC is not just a procedural necessity; it is a cornerstone of responsible project management in safety-critical environments.
Annex A
Example Terms of Reference for Project Safety Committee
Terms of Reference for – Project XXXX
Purpose:
To provide a forum for monitoring and coordinating all safety management and risk reduction activities associated with the project to ensure effective levels of safety and provide an appraisal of the Safety Case. The Project Safety Committee reports to the Project Director or in a larger Delivery Team to the Safety Management Committee.
Tasks:
- Set and keep under review the project’s safety policy and strategy;
- Set and keep under review the project’s safety targets and objectives;
- Define the system boundaries for safety responsibility;
- Advise the Chairperson of the Safety Committee on the safety responsibilities of each authority associated with the project;
- Advise the Chairperson of the Safety Committee on the standards, statutory regulations, and any restrictions with which the projects should comply;
- Review, monitor, classify and allocate new equipment hazards as they are identified;
- Carry out reviews of the project’s Safety Case and progress on achieving safety targets, to a predetermined program, issuing the results to the Delegated Authority;
- Agree on any control measures necessary to reduce identified risks to ALARP;
- Ensure proper and timely availability of training and issue of documentation;
- Carry out actions from ISA, regulatory or internal audit findings;
- Operate a system for reviewing and monitoring safety performance and maintain the Safety Case.
Membership:
- Delivery Team responsible for the procurement aspects of the project;
- Customer representative (Capability or Equipment Customer);
- Safety Officer (if appointed);
- Design organization;
- Delivery Team responsible for the support aspects of the project;
- Equipment User;
- Training Authority;
- Maintainer;
- Maintenance Authority;
- Specialist Advisors (as required):
- Defense Safety Regulators;
- Defense Ordnance Safety Group;
- Land Accident Prevention and Investigation Team;
- Military Aviation Accident Investigation Team;
- Serious Equipment Failure Investigation Team;
- Independent Safety Auditor;
- Interfacing Delivery Teams;
- Technical Specialists.
Acknowledgment of Copyright
In this article, I have used material from a UK Ministry of Defence guide, reproduced under the terms of the UK’s Open Government Licence.
Project Safety Committee: Who Would You Include?
#defstan0056 #DefenseSafetyAuthority #howtoselectsafetycommitteemembers #ProjectManagementSafety #ProjectSafetyCommittee #RiskManagementinEngineering #SafetyCaseManagement #safetycommittee #safetycommitteechairmanresponsibilities #safetycommitteechairpersonresponsibilities #safetycommitteediscussiontopics #safetycommitteegoalsexamples #safetycommitteeiscomprisedof #safetycommitteetermsofreference #safetycommitteevisionstatementexamples #safetyengineering #SafetyManagementCommittee #SafetyOversightinEngineering #systemsafety
Simon Di Nucci
https://www.safetyartisan.com/?p=2354