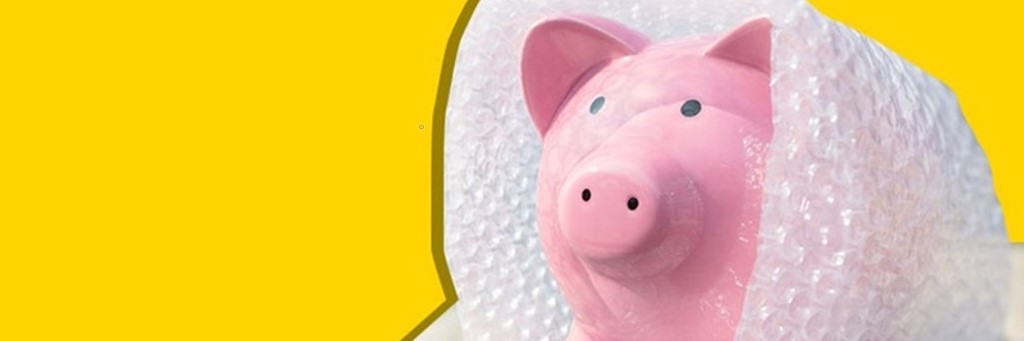
Risk Management 101
Welcome to Risk Management 101, where we're going to go through these basic concepts of risk management. We're going to break it down into the constituent parts and then we're going to build it up again and show you how it's done. I've been involved in risk management, in project risk management, safety risk management, etc., for a long, long time. I hope that I can put my experience to good use, helping you in whatever you want to do with this information.
Maybe you're getting an interview. Maybe you want to learn some basics and decide whether you want to know more about risk management or not. Whatever it might be, I think you'll find this short session really useful. I hope you enjoy it and thanks for watching.
https://youtu.be/dOKALqXYtrg
Welcome to Risk Management 101, where we're going to...
You can get the RM101 Course as part of the FREE Triple Learning Bundle.
Risk Management 101, Topics
- Hazard Identification;
- Hazard Analysis;
- Risk Estimation;
- Risk Evaluation;
- Risk Reduction; and
- Risk Acceptance.
Risk Management 101, Transcript
Click here for the full transcript:
Introduction
Hi everyone and welcome to Risk Management 101. We're going to go through these basic concepts of risk management. We're going to break it down into the constituent parts. Then we're going to build it up again and show you how it's done.
My name is Simon Di Nucci and I have a lot of experience working in risk management, project risk management, safety risk management, etc. I’m hoping that I can put my experience to good use, helping you in whatever you want to do with this information. Whether you're going for an interview or you want to learn some basics. You can watch this video and decide if you want to know more about risk management or you don’t need to. Whatever it might be, you'll find this short session useful. I hope you enjoy it and thanks for watching.
Topics For This Session
Risk Management 101. So what does it all mean? We're going to break risk management down into we've got six constituent parts. I'm using a particular standard that breaks it down this way. Other standards will do this in different ways. We'll talk about that later. Here we've got risk management broken down in to; hazard identification, hazard analysis, risk estimation, risk evaluation (and ALARP), risk reduction, and risk acceptance.
Risk Management
Let's get right on to that. Risk management – what is it? It’s defined as “the systematic application of management policies, procedures and practises to the tasks of hazard identification, hazard analysis, risk estimation, risk and ALARP evaluation, risk reduction, and risk acceptance”.
There are a couple of things to note here. We're talking about management policies, procedures and practices. The ‘how’ we do it. Whether it's a high-level policy or low-level common practice. E.g. how things are done in our organisation vs how the day-to-day tasks are done? And it's also worth saying that when we talk about ‘hazards’, that's a safety ‘ism’. If we were doing security risk management, we can be talking about ‘threats’. We can also be talking about ‘causes’ in day-to-day language. So, we can be talking about something causing a risk or leading to a risk. More on that later, but that's an overview of what risk management is.
Part 1
Let's look at it in a different way. For those of you who like a visual representation, here is a graph of the hierarchical breakdown. They need to happen in order, more-or-less, left to right. And as you can see, there's a link between risk evaluation and risk reduction. We’ll come on to that. So, it's not ‘or’ it’s a serial ‘this is what you have to do’. Sometimes they're linked together more intimately.
Hazard Identification
First of all, hazard identification. So, this is the process where we identify and list hazards and accidents associated with the system. You may notice that some words here are in bold. Where a word is in bold, we are going to give the definition of what it is later.
These hazards could lead to an accident but only associated with the system. That's the scope. If we were talking about a system that was an aeroplane, or a ship, or a computer, we would have a very different scope. There would also be a different way that maybe accidents would happen.
On a more practical level, how do we do hazard identification? I'm not going to go into any depth here, but there are certain classic ones. We can consult with our workers and inspect the workplace where they're operating. And in some countries, that's a legal requirement (Including in Australia where I live). Another option is we can look at historical data. And indeed, in some countries and in some industries, that's a requirement. A requirement means we have to do that. And we can use special analysis techniques. Now, I’m not going to talk about any of those analysis techniques today. You can watch some other sessions on The Safety Artisan to see that.
Hazard Analysis
Having done hazard identification, we've asked ourselves ‘What could go wrong?’. We can put some more detail on and ask, ‘How could it go wrong? And how often?’. That kind of stuff. So, we want to go into more detail about the hazards and accidents associated with this particular system. And that will help us to define some accident sequences. We can start with something that creates a hazard and then the hazard may lead to an accident. And that's what we're talking about. We will show that using graphics late, which will be helpful.
But again, more on terminology. In different industries, we call it different things. We tend to say ‘accident’ in the UK and Australia. In the U.S., they might call it a ‘mishap’, which is trying to get away from the idea that something was accidental. Nobody meant it to happen. Mishap is a more generic term that avoids that implication. We also talk about ‘losses’ or we talk about ‘breaches’ in the security world. We have some issue where somebody has been able to get in somewhere that they should not. And we can talk about accident sequences. Or, in a more common language, we call it a sequence of events. That's all it is.
Risk Estimation
Now we’re talking about the risk estimation. We’ve thought about our hazards and accidents and how they might progress from one to another. Let's think about, ‘How big is the risk of this actually happening?’. Again, we'll unpack this further later at the next level. But for now, we're going to talk about the systematic use of available information. Systematic- so, ordered. We're following a process. This isn't somebody on their own taking a subjective view ‘Look, I think it's not that’. It's a process that is repeatable. We want to do something systematic. It's thorough, it's repeatable, and so it's defendable. We can justify the conclusions that we've come to because we've done it with some rigour. We've done it in a systematic way. That's important. Particularly if we're talking about harm coming to people or big losses.
Risk and ALARP Evaluation
Now, risk evaluation is just taking that estimated risk just now and comparing it to something and saying, “How serious is this risk?”. Is it something that is very low? If it's very insignificant then we're not bothered about it. We can live with it. We can accept it. Or is it bigger than that? Do we need to do something more about it? Again, we want to be systematic. We want to determine whether risk reduction is necessary. Is this acceptable as it is or is it too high and we need to reduce it? That's the core of risk evaluation.
In this UK-based standard – we're using terminology is found in different forms around the world. But in the UK, they talk about ‘tolerability’. We're talking about the absolute level of risk. There probably is an upper limit that's allowed in the law or in our industry. And there's a lower limit that we're aiming for. In an ideal world, we'd like all our risks to be low-level risks. That would be terrific.
So, that's ‘tolerability’. And you might hear it called different things. And then within the UK system, there're three classes of ‘tolerability’ at risk. We could say it's either ‘broadly acceptable’- it’s very low. It’s down in the target region where we like to get all our risks. It's ‘tolerable’- we can expose people to this risk or we can live with this risk, but only if we've met certain other criteria. And then there's the risk that it's so big. It’s so far up there, we can't do that. We can't have that under any circumstances. It's unacceptable. You can imagine a traffic light system where we have categorised our risk.
And then there’s the test of whether our risk can be accepted in the UK. It's called ALARP. We reduce the risk As Low As Reasonably Practicable. And in other places, you’ll see SFARP. We've eliminated or minimised the risk So Far As Is Reasonably Practicable. In the nuclear industry, they talk about ALARA: As Low As Reasonably Achievable. And then different laws use different tests. Whichever one you use, there's a test that we have got to use to say, “Can we accept the risk?” “Have we done enough risk reduction?”. And whatever you've put in those square brackets, that's the test that you're using. And that will vary from jurisdiction to jurisdiction. The basic concept of risk evaluation is estimating the level of risk. Then compare it to some standard or some regulation. Whatever one it might be, that's what we do. That's risk evaluation.
Risk Reduction
We’ve asked, “Do we need to reduce risk further?”. And if we do, we need to do some risk reduction. Again, we’re being systematic. This is not some subjective thing where we go “I have done some stuff, it'll be alright. That's enough.”. We're being a bit more rigorous than that. We've got a systematic process for reducing risk. And in many parts of the world, we’re directed to do things in a certain way.
This is an illustration from an Australian regulation. In this regulation, we're aiming to eliminate risk. We want to start with the most effective risk reduction measures. Elimination is “We’ve reduced the risk to zero”. That would be lovely if we could do that but we can't always do that.
What's the next level? We could get rid of this risk by substituting something less risky. Imagine we've got a combustion engine powering something. The combustion engine needs flammable fuel and it produces toxic fumes. It could release carbon monoxide and CO2 and other things that we don't want. We ask, “Can we get rid of that?”. Could we have an electric motor instead and have a battery instead? That might be a lot safer than the combustion engine. That is a substitution. There are still risks with electricity. But by doing this we've substituted something risky for something less risky.
Or we could isolate the hazard. Let’s use the combustion engine as an example again. We can say, “I'll put that in the fuel and the exhaust somewhere, a long way from people”. Then it’ll be a long way from where it can do harm or cause a loss.” And that's another way of dealing with it.
Or we could say, “I'm going to reduce the risks through engineering controls”. We could put in something engineered. For example, we can put in a smoke detector. A very simple, therefore highly reliable, device. It’s certainly more reliable than a human. You can install one that can detect some noxious gases. It's also good if it’s a carbon monoxide detector. Humans cannot detect carbon monoxide at all. (Except if you've got carbon monoxide poisoning, you'll know about it. Carbon monoxide poisoning gives you terrible headaches and other symptoms.) But of course, that's not a good way to detect that you're breathing in poisonous gas. We do not want to do it that way.
So, we can have an engineering control to protect people. Or we can an interlock. We can isolate things in a building or behind a wall or whatever. And if somebody opens the door, then that forces the thing to cut out so it's no longer dangerous. There are different things for engineering controls that we can introduce. They do not rely on people. They work regardless of what any person does.
Next on the list, we could reduce exposure to the hazard by using administrative controls. That's giving somebody some rules to follow a procedure. “Do this. Don't do that.” Now, that's all good. We can give people warning signs and warn people not to approach something. But, of course, sometimes people break the rules for good reasons. Maybe they don't understand. Or, maybe they don't know the danger. Maybe they've got to do something or maybe the procedure that we've given them doesn't work very well. It's too difficult to get the job done, so people cut corners. So, procedural protection can be weak. And a bit hit and miss sometimes.
And then finally, we can give people personal protective equipment. We can give them some eye protection. I'm wearing glasses because I'm short-sighted. But you can get some goggles to protect your eyes from damage. Damage like splashes, flying fragments, sparks, etc. We can have a hard hat so that if we’re on a building site and something drops from above on us that protects the old brain box. It won't stop the accident from happening, but it will help reduce the severity of the accident. That's the least effective. We're doing nothing to prevent the accident from happening. We're reducing the severity in certain circumstances. For example, if you drop a ton of bricks on me, it doesn't matter whether I'm wearing a hard hat or not. I'm still going to get crushed. But with one brick, I should be able to survive that if I'm wearing a hard hat.
Risk Acceptance
Let's move on to risk acceptance. At some stage, if we have reduced the risk to a point where we can accept it. We can live with it and we’ve decided that we're going to need to do whatever it is that is exposing us to the risk. Let's use the system: get in our car to enable us to go from a to b quickly and independently. So, we're going to accept the risk of driving in our car. We’ve decided we're going to do that. We make risk acceptance decisions every day, often without thinking about it. We get in a car every day on average and we don't worry about the risk, but it's always there. We've just decided to accept it.
But in this example we've got, it's not an individual deciding to do something on the spur of the moment. Nor is it based on personal experience. We've got a systematic process where a bunch of people come together. The relevant stakeholders agree that a risk has been assessed or has been estimated and has been evaluated. They agree that the risk reduction is good enough and that we will accept that risk. There’s a bit more to it than you and I saying, “That'll be alright.”
Part 2
Let's summarise where we’ve got to. We've talked about these six components of risk management. That's terrific. And as you can see, they all go together. Risk evaluation and risk reduction are more tightly coupled. That’s because when we do some risk reduction, we then re-evaluate the risk. We ask ‘Can we accept it?’. If the answer is ‘No.’ we need to do some more work. Then we do some more risk reduction. So those tend to be a bit more coupled together at the end. That's the level we've got to. We're now going to go to the next level.
So, we're going to explain these things. We've talked about hazard identification and hazard analysis, but what is a hazard? And what is an accident? And what is an accident sequence? We're going to unpack that a bit more. We’re going to take it to the next level. And throughout this, we're talking about risk over and over again. Well, what is ‘risk’? We're going to unpack that to the next level as well. It all comes down to this anyway. This is a safety standard. We're talking about harm to people. How likely is that harm and how severe might it be? But it might be something else. It might be a loss or a security breach. A financial loss. It might be a negative result for our project. We might find ourselves running late. Or we're running over budget. We’re failing to meet quality requirements. Or we’re failing to deliver the full functionality that we said we would. Whatever it might be.
Hazard
So, let's unpack this at the next level. A hazard is a term that we use, particularly in safety. As I say, we call it other things in different realms. But in the safety world, it's a physical situation or it's a state of a system. And as it says, it often follows from some initiating event which we may call a ‘cause’. The hazard may lead to an accident. The key thing to remember is once a hazard exists, an accident is possible, but it's not certain. You can imagine the sort of cartoon banana skin on the pavement gag. Well, the banana skin is the hazard. In the cartoon, the cartoon character always steps on the banana skin. They always fall over the comic effect. But in the real world, nobody may tread on the banana skin and slip over. There could be nobody there to slip over all the banana skin. Or even if somebody does, they could catch themselves. Or they fall, but it's on a soft surface and they don't hurt themselves so there's no harm.
So, the accident isn't certain. And in fact, we can have what we call ‘non-accident’ outcomes. We can have harmless consequences. A hazard is an important midway step. I heard it called an accident waiting to happen, which is a helpful definition. An accident waiting to happen, but it doesn't mean that the accident is inevitable.
Accident
But the accident can happen. Again, the ‘accident’, ‘mishap’, or ‘unintended event’. Something we did not want or a sequence of events that causes harm. And in this case, we're talking about harm to people. And as I say, it might be a security breach. It might be a financial loss. It might be reputational damage. Something might happen that is very embarrassing for an organisation or an individual. Or again, we could have a hiccup with our project.
Harm
But in this case, we're talking about harm. And this kind of standard, we're using what you might call a body count approach to the harm. We're talking about actual death, physical injury, or damage to the health of people. This standard also considers the damage to property and the environment. Now, very often we are legally required to protect people and the environment from harm. Property less so. But there will be financial implications of losses of property or damage to the systems. We don't want that. But it's not always criminally illegal to do that. Whereas usually, hurting people and damaging the environment is. So, this is ‘harm’. We do not want this thing to happen. We do not want this impact. Safety is a much tougher business in this instance. If we have a problem with our project, it’s embarrassing but we could recover it. It’s more difficult to do that when we hurt somebody.
Risk
And always in these terms, we're talking about ‘risk’. What is ‘risk’? Risk is a combination of two things. It's a combination of the likelihood of harm or loss and the severity of that harm or loss. It’s those two things together. And we've got a very simple illustration here, a little table. And they're often known as a risk matrix, but don’t worry about that too much. Whatever you want to call it. We've got a little two by two table here and we've got likelihood in the white text and severity in the black. We can imagine where there's a risk where we have a low likelihood of a ‘low harm’ or a ‘low impact’ accident or outcome. We say, ‘That's unlikely to happen and even if it does not much is going to happen.’ It’s going to be a very small impact. So, we'd say that that's a low risk.
Then at the other end of the spectrum, we can imagine something that has a high likelihood of happening. And that likelihood also has a high impact. Things that happen that we definitely do not want to happen.
#howtoriskmanagement #howtoriskmanagementanalysis #isriskmanagement #learnriskmanagement #learnriskmanagementanalysis #riskmanage #riskmanagedframework #riskmanagement #riskmanagementanalysistechnique #riskmanagementanalysistraining #riskmanagementanalysistutorial #riskmanagementdefinition #riskmanagementframework #riskmanagementplan #riskmanagementprocess #riskmanagementtechnique #riskmanagementtraining #riskmanagementtutorial #riskmanagementvideo #riskmanager #whatriskmanagement
Simon Di Nucci
https://www.safetyartisan.com/2021/05/14/risk-management-101/