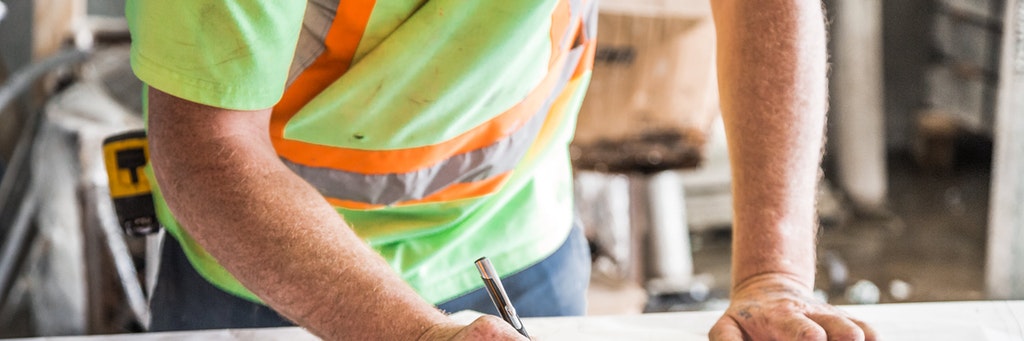
Good Work Design
Good work design can help us achieve safe outcomes by designing safety into work processes and the design of products. Adding safety as an afterthought is almost always less effective and costs more over the lifecycle of the process or product.
Introduction
The Australian Work Health and Safety Strategy 2012-2022 is underpinned by the principle that well-designed healthy and safe work will allow workers to have more productive lives. This can be more efficiently achieved if hazards and risks are eliminated through good design.
Work is currently underway by Safe Work Australia to update the WHS Strategy for 2022-2032. Top Tip
The Ten Principles of Good Work Design
This handbook contains ten principles that demonstrate how to achieve the good design of work and work processes. Each is general in nature so they can be successfully applied to any workplace, business, or industry.
The ten principles for good work design are
structured into three sections:
- Why good work design is important;
- What should be considered in good work design; and
- How good work is designed.
These principles are shown in the diagram in Figure 1.
Figure 1. Good work design principles.
This handbook complements a range of
existing resources available to businesses and work health and safety
professionals including guidance for the safe design of plant and structures
see the Safe Work Australia Website.
Scope of the Handbook
This handbook provides information on how to apply good work design principles to work and work processes to protect workers and others who may be affected by the work.
It describes how design can be used to set up the workplace, working environment, and work tasks to protect the health and safety of workers, taking into account their range of abilities and vulnerabilities, so far as reasonably practicable.
The handbook does not aim to provide advice on managing situations where individual workers may have special requirements such as those with a disability or on a return to work program following an injury or illness.
Who Should Use this Handbook?
This handbook should be used by those with
a role in designing work and work processes, including:
- Persons conducting a business or undertaking (PCBUs) with a primary duty of care under the model Work Health and Safety (WHS) laws.
- PCBUs who have specific design duties relating to the design of plant, substances, and structures including the buildings in which people work.
- People responsible for designing organizational structures, staffing rosters, and systems of work.
- Professionals who provide expert advice to organizations on work health and safety matters.
Good work design optimizes work health and safety, human performance, job satisfaction, and business success.
Information: Experts who provide advice on the design of work may include: engineers, architects, ergonomists, information, and computer technology professionals, occupational hygienists, organizational psychologists, human resource professionals, occupational therapists, and physiotherapists.
What is ‘Good Work’?
‘Good work’ is healthy and safe work where the hazards and risks are eliminated or minimized so far as is reasonably practicable. Good work is also where the work design optimizes human performance, job satisfaction, and productivity.
Good work contains positive work elements that
can:
- protect workers from harm to their health, safety, and welfare;
- improve worker health and wellbeing; and
- improve business success through higher worker productivity.
What is Good Work Design?
The most effective design process begins at the earliest opportunity during the conceptual and planning phases. At this early stage there is the greatest chance of finding ways to design-out hazards, incorporate effective risk control measures, and design-in efficiencies.
Effective design of good work considers:
The work:
- how work is performed, including the physical, mental and emotional demands of the tasks and activities
- the task duration, frequency, complexity, and
- the context and systems of work.
The physical working
environment:
- the plant, equipment, materials, and substances used, and
- the vehicles, buildings, and structures that are workplaces.
The workers:
- physical, emotional, and mental capacities and needs.
Effective design of good work can radically transform the workplace in ways that benefit the business, workers, clients, and others in the supply chain.
Failure to consider how work is designed can result in poor risk management and lost opportunities to innovate and improve the effectiveness and efficiency of work.
I suspect that many of us have seen badly-designed work, which results in workarounds or waste, or both. A little fore-thought can prevent this.Top Tip
The principles for good work design
support duty holders to meet their obligations under the WHS laws and also help
them to achieve better business practice generally.
For the purposes of this handbook, a work designer is anyone who makes decisions about the design or redesign of work. This may be driven by the desire to improve productivity as well as the health and safety of people who will be doing the work
The WHY Principles
Why is good work design important?
Principle 1: Good
work design gives the highest level of protection so far as is reasonably
practicable
- All workers have a right to the highest practicable level of protection against harm to their health, safety, and welfare.
- The primary purpose of the WHS laws is to protect persons from work-related harm so far as is reasonably practicable.
- Harm relates to the possibility that death, injury, illness, or disease may result from exposure to a hazard in the short or long term.
- Eliminating or minimizing hazards at the source before risks are introduced in the workplace is a very effective way of providing the highest level of protection.
Principle 1 refers to the legal duties under the WHS laws. These laws provide the framework to protect the health, safety, and welfare of workers and others who might be affected by the work. During the work design, process workers and others should be given the highest level of protection against harm that is reasonably practicable.
Prevention of workplace
injury and illness
Well-designed work can prevent work-related deaths, injuries, and illnesses. The potential risk of harm from hazards in a workplace should be eliminated through good work design.
Only if that is not reasonably practicable, then the design process should minimize hazards and risks through the selection and use of appropriate control measures.
New hazards may inadvertently be created when changing work processes. If the good work design principles are systematically applied, potential hazards and risks arising from these changes can be eliminated or minimized.
Information: Reducing the speed of an inappropriately fast process line will not only reduce production errors, but can also diminish the likelihood of a musculoskeletal injury and mental stress.
Principle 2: Good
work design enhances health and wellbeing
- Health is a “state of complete physical, mental, and social wellbeing, not merely the absence of disease or infirmity” (World Health Organisation).
- Designing good work can help improve health over the longer term by improving workers’ musculoskeletal condition, cardiovascular functioning, and mental health.
- Good work design optimizes worker function and improves participation enabling workers to have more productive working lives.
Health
benefits
An effective design aims to prevent harm, but it can also positively enhance the health and wellbeing of workers, for example, satisfying work and positive social interactions can help improve people’s physical and mental health.
As a general guide, the healthiest workers have been found to be three times more productive than the least healthy. It, therefore, makes good business sense for work design to support people’s health and wellbeing.
Information: Recent research has shown long periods of sitting (regardless of exercise regime) can lead to an increased risk of preventable musculoskeletal disorders and chronic diseases such as diabetes. In an office environment, prolonged sitting can be reduced by allowing people to alternate between sitting or standing whilst working.
Principle 3: Good
work design enhances business success and productivity
- Good work design prevents deaths, injuries, and illnesses and their associated costs, improves worker motivation and engagement, and in the long-term improves business productivity.
- Well-designed work fosters innovation, quality, and efficiencies through effective and continuous improvement.
- Well-designed work helps manage risks to business sustainability and profitability by making work processes more efficient and effective and by improving product and service quality.
Cost savings and productivity improvements
Designing-out problems before they arise is generally cheaper than
making changes after the resulting event, for example by avoiding expensive
retrofitting of workplace controls.
Good work design can have direct and tangible cost savings by
decreasing disruption to work processes and the costs from workplace injuries
and illnesses.
Good work design can also lead to productivity improvements and
business sustainability by:
- allowing organizations to adjust to changing business needs and streamline work processes by reducing wastage, training, and supervision costs
- improving opportunities for creativity and innovation to solve production issues, reduce errors and improve service and product quality, and
- making better use of workers’ skills resulting in more engaged and motivated staff willing to contribute greater additional effort.
Figure 1, The WHY Principles
The WHAT Principles
What should be considered by those with design
responsibilities?
Principle 4: Good work design addresses physical, biomechanical, cognitive, and psychosocial characteristics of work, together with the needs and capabilities of the people involved
- Good work design addresses the different hazards associated with work e.g. chemical, biological, and plant hazards, hazardous manual tasks, and aspects of work that can impact mental health.
- Work characteristics should be systematically considered when work is designed, redesigned or the hazards and risks are assessed.
- These work characteristics should be considered in combination and one characteristic should not be considered in isolation.
- Good work design creates jobs and tasks that accommodate the abilities and vulnerabilities of workers so far as reasonably practicable.
All tasks have key characteristics with associated hazards and risks, as shown in Figure 2 below:
Figure 2 – Key characteristics of work.
Hazards and risks associated with tasks are identified and
controlled during good work design processes and they should be considered in
combination with all hazards and risks in the workplace. This highlights that
it is the combination that is important for good work design.
Workers can also be exposed to a number of different hazards from a single task. For example, meat boning is a common task in a meat-processing workplace. This task has a range of potential hazards and risks that need to be managed, e.g. physical, chemical, biological, biomechanical, and psychosocial. Good work design means the hazards and risks arising from this task are considered both individually and collectively to ensure the best control solutions are identified and applied.
Good work design can prevent unintended consequences which might arise if task control measures are implemented in isolation from other job considerations. For example, automation of a process may improve production speed and reduce musculoskeletal injuries but increase the risk of hearing loss if effective noise control measures are not also considered.
Workers have different needs and capabilities; good work design
takes these into account. This includes designing to accommodate them given the
normal range of human cognitive, biomechanical and psychological
characteristics of the work.
Information: The Australian workforce is changing. It is typically older with higher educational levels, more inclusive of people with disabilities, and more socially and ethnically diverse. Good work design accommodates and embraces worker diversity. It will also help a business become an employer of choice, able to attract and retain an experienced workforce.
Principle 5: Good work design considers the business needs, context, and work environment.
- Good work design is ‘fit for purpose’ and should reflect the needs of the organization including owners, managers, workers, and clients.
- Every workplace is different so approaches need to be context-specific. What is good for one situation cannot be assumed to be good for another, so off-the-shelf solutions may not always suit every situation.
- The work environment is broad and includes: the physical structures, plant and technology, work layout, organizational design and culture, human resource systems, work health and safety processes, and information/control systems.
The business organizational structure and culture, decision-making processes, work environment, and how resources and people are allocated to the work will, directly and indirectly, impact on work design and how well and safely the work is done.
The work environment includes the physical structures, plant, and technology. Planning for relocations, refurbishments, or when introducing new engineering systems are ideal opportunities for businesses to improve their work designs and avoid foreseeable risks.
These are amongst the most common work
changes a business undertakes yet good design during these processes is often
quite poorly considered and implemented. An effective design following the
processes described in this handbook can yield significant business benefits.
Information: Off-the-shelf solutions can be explored for some common tasks, however usually design solutions need to be tailored to suit a particular workplace.
Good work design is most effective when it
addresses the specific business needs of the individual workplace or business.
Typically work design solutions will differ between small and large businesses.
However, all businesses must eliminate or minimize their work health and safety risks so far as reasonably practicable. The specific strategies and controls will vary depending on the circumstances.
The table on the next page demonstrates
how to step through the good work design process for small and large
businesses.
Good design steps In a large business that is downsizing In a small business that is undergoing a refit
Management commitment
Senior management make their commitment to good work design explicit ahead of downsizing and may hire external expertise. The owner tells workers about their commitment to designing-out hazards during the upcoming refit of the store layout to help improve safety and efficiency.
Consult
The consequences of downsizing and how these can be managed are discussed in senior management and WHS committee meetings with appropriate representation from affected work areas. The owner holds meetings with their workers to identify possible issues ahead of the refit.
Identify
A comprehensive workload audit is undertaken to clarify opportunities for improvements. The owner discusses the proposed refit with the architect and builder and gets ideas for dealing with issues raised by workers.
Assess
A cost-benefit analysis is undertaken to assess the work design options to manage the downsizing. The owner, architect, and builder jointly discuss the proposed refit and any worker issues directly with workers.
Control
A change management plan is developed and implemented to appropriately structure teams and improve systems of work. Training is provided to support the new work arrangements. The building refit occurs. Workers are given training and supervision to become familiar with a new layout and safe equipment use.
Review
The work redesign process is reviewed against the project aims by senior managers. The owner checks with the workers that the refit has improved working conditions and efficiency and there are no new issues.
Improve
Following consultation, refinement of the redesign is undertaken if required. Minor adjustments to the fit-out are made if required. Table 1 – steps in good work design for large and small businesses
Principle 6: Good
work design is applied along the supply chain and across the operational
lifecycle.
- Good work design should be applied along the supply chain in the design, manufacture, distribution, use and disposal of goods and the supply of services.
- Work design is relevant at all stages of the operational life cycle, from start-up, routine operations, maintenance, downsizing and cessation of business operations.
- New initiatives, technologies, and changes in organizations have implications for work design and should be considered.
Information: Supply chains are often made up of complex commercial or business relationships and contracts designed to provide goods or services. These are often designed to provide goods or services to a large, dominant business in a supply chain. The human and operational costs of poor design by a business can be passed up or down the supply chain.
Businesses in the supply chain can have
significant influence over their supply chain partners’ work health and safety
through the way they design the work.
Businesses may create risks and so they
need to be active in working with their supply chains and networks to solve
work health and safety problems and share practical solutions for example, for
common design and manufacturing problems.
Health and safety risks can be created at
any point along the supply chain, for example, loading and unloading causing
time pressure for the transport business.
There can be a flow-on effect where the
health and safety and business ‘costs’ of poor design may be passed down the
supply chain. These can be prevented if businesses work with their supply chain
partners to understand how contractual arrangements affect health and safety.
Procurement and contract officers can also positively influence their own organization and others' work health and safety throughout the supply chain through the good design of contracts.
When designing contractual arrangements
businesses could consider ways to support good work design safety outcomes by:
- setting clear health and safety expectations for their supply chain partners, for example through the use of codes of conduct or quality standards
- conducting walk-through inspections, monitoring, and comprehensive auditing of supply chain partners to check adherence to these codes and standards
- building the capability of their own procurement staff to understand the impacts of contractual arrangements on their suppliers, and
- consulting with their supply chain partners on the design of good work practices.
Information: The road transport industry is an example of the application of how this principle can help improve drivers’ health and safety and address issues arising from supply chain arrangements. For example, the National Heavy Vehicle Laws ‘chain of responsibility’ requires all participants in the road transport supply chain to take responsibility for driver work health and safety. Contracts must be designed to allow drivers to work reasonable hours, take sufficient breaks from driving and not have to speed to meet deadlines.
#10principleofgooddesign #bestdesignwords #gooddesignideas #gooddesignprinciples #goodworkdesign #howtosafedesign #howtosafedesignanalysis #learnsafedesign #learnsafedesignanalysis #Safebydesignprinciples #safedesignanalysistechnique #safedesignanalysistraining #safedesignanalysistutorial #safedesigntechnique #safedesigntraining #safedesigntutorial #safedesignvideo #safetyprinciples #whatiseffectivedesign
Simon Di Nucci https://www.safetyartisan.com/2022/05/11/good-work-design/