Consultation, Cooperation & Coordination CoP
In this 30-minute session, we look at the Consultation, Cooperation & Coordination Code of Practice (CC&C CoP). We cover the Commonwealth and Model versions of the CoP, appendices & a summary of detailed requirements; and further commentary. This CoP is one of the two that are generally applicable.
https://youtu.be/CARK4tJnX28
This is the three-minute demo of the full, 30-minute video.
buy the full-length video here
Consultation, Cooperation & Coordination CoP: Topics
- CC&C in the Federal or Commonwealth CoP;
- Extra CC&C in the Model CoP;
- (Watch out for Jurisdiction);
- Further commentary; and
- Where to get more information.
Consultation, Cooperation & Coordination CoP: Transcript
Click Here for the Transcript
Consultation, Cooperation & Coordination CoP
Hello, everyone, and welcome to The Safety Artisan. I'm Simon and today we're going to be talking about a very useful subject, which is Codes of Practice. And one Code of Practice in particular, which is the Code of Practice for Consultation, Cooperation and Coordination. And it doesn't sound like the most exciting subject, I'll admit, but this is one of only two Codes of Practice that you must be aware of if operating in Australia, or exporting to Australia, or importing stuff to Australia, whatever it might be. The other Code of Practice that you must be aware of is the Risk Management Code of Practice. There are a lot more Code of Practices than these two, but they don't always apply. So, I mean if you're not doing anything to do with asbestos, you don't have to worry about what it says in the Asbestos Code of Practice. But this one you do because it applies to everything.
Topics for this Session
And I've used this Code of Practice to help clients and to do particular things and help everybody understand what we have to do, and it’s very useful. And in this session, I will be explaining how to get the best out of this Code of Practice and, at the end, where to get more information. So, I hope you'll find that useful. So we're going to be talking about the - I'm just going to call it the C, C & C CoP for short because it's a dreadful mouthful, isn't it? We're going to be looking at the federal or Commonwealth Code of Practice and then we're going to look at some extras in the Model Code of Practice. So just to explain that briefly, the Model Code of Practice is on the Safe Work Australia website, and that is the Model from which all other CoPs are developed. However, Safe Work Australia is not a regulator. So individual regulators and the example I'm using is the Commonwealth one- or Comcare, as it's known- they have chosen to edit the Model CoP and change it and remove quite a bit of material. Now, why they chose to do that, I do not know. So, you have to be careful which jurisdiction you're operating in, in Australia. If you are in a Commonwealth workplace, then you need to apply the Commonwealth or the federal version of WHS, including this CoP. And if you're in a state or territory workplace, or a commercial workplace in a state or territory, you need to apply the relevant one there. And just to complicate matters, Western Australia has not yet introduced WHS and Victoria has no plans to do so. So, of course, in Australia, we like to make life simple for ourselves, don't we? Oh no, we don't!
So after I've gone through some basics of what's in the CoP, because you'll see there's an awful lot of material in there that I'm not going to talk about. I produced some commentary that I think you will find helpful and where to get more information, as I promised. So, let's get on with it!
When to Consult
So, first of all- and you'll notice that I'm only including those bits really that say when you must do something. So, this is quoting Section 49 of the WHS Act, which says that if you're conducting a business or some kind of undertaking- so it's not just a commercial business, but anything- you must consult with your workers when identifying hazards and assessing risks, making decisions about how you're going to control those risks, making decisions about the adequacy of facilities for welfare, proposing changes that affect health and safety, and making decisions about procedures for consulting with workers, providing information and training, and so on and so forth. So, there's a whole raft of things that you have to consult your workers on. So, this is all workplace so far. Now, in my role as a safety consultant, I'm often working with people who are introducing they're buying bits of kit, or designing or importing bits of kit, and there is no work yet, so there's no workers. But we always try and get a representative of the end-user involved because that really does help you do good quality safety work and avoid- to be honest- wasting time and money on things that are theoretically possible or theoretically sound problematic but in reality, it just doesn't arise for whatever reason. So, I really do recommend getting those end-user representatives involved.
Effective Consultation
And if we go on to Section 48- for some reason, the cop quotes these things in reverse order- to be effective in consultation, we require information to be shared. Workers have got to have a reasonable opportunity to express their views. They've got to have a reasonable opportunity to contribute to decisions. Their views must be taken into account and they must be advised of the outcomes of consultation. So, all good common-sense stuff, I would think. Nothing controversial about this and that- to be honest- that's a feature of CoPs. They tell you to do things that you think, “Yeah, I really ought to be doing that!”.
Consultation Procedures
Continuing with the countdown, we're on to Section 47. Consultation procedures, again more basic common sense. If you’ve agreed to procedures for consultation, you must follow those procedures. It's not rocket science, is it, folks? Let's move on.
Sections 16 & 46
OK, now this is a bit more interesting, I think. This is getting into the real guts of this Code of Practice because where consultation, cooperation and coordination really come into play is where you've got multiple stakeholders, multiple duty holders- that is to say, those with a duty to protect the health and safety of people. Where multiple stakeholders, duty holders, have to get together and work together in order to come up with a solution. So the law says- Section 16 says where more than one person has a duty for the same thing, for the same matter, each person retains that responsibility. You cannot wriggle out of your responsibility just because you only control a bit over here and not over here. So, the two duty holders who have control here and here, they have to work together. The law says so. And so this is really the guts of this Code of Practice. And they must work together to discharge their duties to the extent to which they can. And the extent to which you can is the extent to which you influence and control the matter. So, WHS law is very big about control. If you have control of the bit, you've got to do your bit and you must work with people who have control of other things. You might be designing or buying a piece of kit. Other people might control the workplace. There might be another group of people who represent the operators, and then another group who represent the maintainers, and so on and so forth. They've all got to be involved if they're relevant to managing risk. And of course, as risk in WHS is cradle to grave, then pretty much everyone is involved.
So, Section 46, and in these situations where you have got multiple duty holders, each person with a duty must, so far as is reasonably practicable, consult, cooperate and coordinate with all other persons. And I'm going to do a session quite soon on so far as is reasonably practicable, or SOFARP, and in it, I will tell you that SOFARP is an objective test and the law sets objective expectations for what a reasonable person would do. So, you can't just say, “Well, I'll decide what is reasonable or not reasonable.”. The law has already done it for you and there's guidance out there to help you so follow it. So, we will do something on that guidance, about what is reasonable and what is reasonably practicable. But we've got to work with each other SOFARP. For the greater good! Sorry, that's a quote from one of my favourite comedy films, by the way.
CoP Appendices
So, appendices to the CoP. If we look at the appendices in the federal or Commonwealth CoP, there are only three. So, they've got some examples of arrangements. They've got a consultation checklist, and they've got an appendix on C, C and C activities, which is all good. That's all good stuff. In addition, if you go back to the Model Code of Practice, you will find that there's also a glossary. Yes, they've got the consultation checklist. And then in Appendix E, you've got a summary of all the consultation requirements in the WHS regulations, which is really useful. So even if in the CoP that applies to you, your version of the CoP doesn't have the appendix, I would recommend going and having a look in the Model CoP. And if you're not aware what you got, if you've got a high-risk business, then you're going to find some extra requirements in the regulations. So, I would go and have a look at Appendix E if you're doing anything that could kill one or more people. So, if you're dealing with more serious risks, then I would go and have a look at that just to- as a good lead in to the regulations. If you already know the regulations backwards, then great, you don't need to bother. But there are over 600 regulations in WHS, so it's always worth checking up to make sure you haven't missed anything.
Extras in the Model CoP
We've kind of started already, but now we've really started we're going to talk about the extras in the Model Code of Practice.
Further Duties of PCBUs
In the modal Code of Practice, we get a reminder that designers, manufacturers, importers and suppliers have got safety responsibilities to ensure, so far as is reasonably practicable, that the plant's substance or structure that they are designing, etc, etc, is without risks to health and safety. And they've got a duty to carry out testing and analysis and to provide specific safety-related information about plant or substance. So there's a good reminder in there that we all, wherever we are in the supply chain, we've all got these responsibilities. And to assist in meeting these duties, the WHS regulations require manufacturers to consult with designers, importers to consult with designers and manufacturers, and whoever commissions construction work to consult with the designer of the structure, for example. There's a lot of useful extra pointers in the Model Code of Practice, which may not be in the version that, technically speaking/strictly speaking, you have to follow. So, worth a look.
Officers (of the PCBU)
And then there's also a reminder to officers of the business or undertaking. Basically, officers says- for example, company directors, those kinds of people, have a duty to exercise due diligence. And you have to go look at due diligence to see what that is. There are basically six bullet points in the act that describe due diligence. Again, it's all good common-sense stuff. There’s nothing esoteric in there or objectionable. And that due diligence includes taking reasonable steps to ensure that you've got appropriate processes for complying with the duty to consult as well as to duty- with workers sorry, as well as consulting, cooperating and coordinating with other duty holders. And there's further guidance on what's an officer in that interpretive guideline and under Section 27 of the law.
Principal Contractors
And then here is one I picked out. I've not got all of the requirements, but here's a useful one. There’s a particular regulation, number 309, that says if you're doing construction work the principal contractor for a construction project has a specific duty under WHS regulations to document in their WHS management plan the arrangements for consultation, cooperation and coordination. Now that's not unique, as we've just seen, to construction, but there is a specific requirement in there for a principal contractor. And WHS assumes a particular structure where you've got a prime contractor, or a principal contractor, who is leading the construction for the customer. So, have a look at that. There's also a CoP on the construction of structures so if you're in that game you'll find that useful too.
Major Hazard Facilities
And then I've got one slide on major hazard facilities. Now, a major hazard facility, strictly speaking, is a facility where you've got enough of a dangerous chemical- and it might be flammable, it might be toxic, it might be explosive, whatever it is. There's a whole list of chemicals in the regulations and it says if you've got so many tons of this or that, you've hit the threshold and you are operating a major hazard facility. There's a whole raft of extra regulations that apply to MHFs. And it says, for example, regulation 552 requires a major facility- sorry, a major hazard facilities safety case outline- so a safety case report by another name- to include a description of the consultation with workers that's been undertaken in the preparation of the safety case. Again, you've got a very specific requirement to consult with workers and to document it. Which, interestingly enough, generally, you don't have a duty to do that. It's not mandatory to document consultation. It's recommended. It's a good idea but you don't, strictly speaking, have to do it unless you're operating an MHF. And as it says there, there's a whole bunch of regulations that cover consultation about MHFs. But as I said, if you look at Appendix E of the Model Code of Practice, it's got them all listed, which is very helpful.
Detailed Requirements
A quick word about detailed requirements. Every Code of Practice contains detailed requirements that follow this formula. So, there are three words that indicate a legal requirement that must be complied with. And those three words are ‘must’, ‘requires’- or variations on that word-, and ‘mandatory’. So, any instances of those words- Probably not always, because they occasionally you come across a usage of ‘must’ or ‘requires’ where you go “Actually, that's just an English use-“ (if you know what I mean)- “That’s just an English use of those words! It’s not really indicating a mandatory requirement”. But most of them do. So, in the Commonwealth Code of Practice, we have 41 instances of ‘must’. So, you've got to comply with those. You have 46 instances of ‘require’ and you've got to comply with those by law. Now, interestingly, in the Model Code of Practice, those numbers go up to 71 and 58, respectively. So, there're a lot more requirements in the Model Code of Practice. So, again, do make sure you've got the right Code of Practice that's been issued by the regulator for your jurisdiction. Because otherwise you might miss something you need to comply with or you might be complying with something that, strictly speaking, you don't have to. Although, of course, it's not a bad thing to do that but you don't have to.
Then there's the use of the word ‘should’, which is a recommended course of action, and ‘may’, suggests something that is optional. And again, in the Commonwealth Code of Practice, there are 62 instances of ‘should’ and 86 of ‘may’. Although I note that one of those instances of may, at least one, refers to the month of May when that Code of Practice was published. So, you've got to go through and make sure that they are relevant. And then it's slightly more in the Model Code of Practice. It’s 66 and 90, respectively. But the difference is not so great for the mandatory stuff. Now as I've said before, and in the risk management Code of Practice, my advice to you is you must comply with ‘musts’ and ‘required’s. ‘Should’ is recommendation so I would suggest complying with that unless you've got a good reason not to. In which case, I would document the fact that you've got a good reason not to and why you're not going to. And then ‘may’ is optional. You can do it if you want to and you can record the fact that you've considered those things and reject them if you want to but they are only options. So, I think there's- effectively we've got three tiers here. We've got ‘must comply’, ‘recommended’, and ‘you can do this if you think it's a good idea’.
And so the comment at the bottom, CoPs are not huge documents that typically a few tens of pages long. They will repay careful reading because you do have to comply with quite a lot of stuff that's in there and that's very clearly signposted, by the way. And also, of course, this particular Code of Practice is very useful for safety management plans. If you've got to write a safety management plan and you want to know what you have to include in it, then look in this Code of Practice and look in the Risk Management Code of Practice and make sure you include everything that is mandatory or ‘must’ or ‘requires’ and look at all the other stuff as well. And why not? If the copyright permits you to do so, which it usually does- not always, but usually. If the copyright permits you to do so and just copy and paste the stuff into your plan and then you know that you've got what you need. Then you can change the wording if you need to. But it will save you a lot of bother if you've got to write a safety management plan. It'll help you to make sure you've got everything you need to and it will save you a lot of effort. So, I recommend that I've done that myself.
Commentary #1
I think I've just got a couple of slides of commentary. It's worth reiterating that Codes of Practice are for all Australian industry. Whether it be a sole trader like myself operating out of our study or their garage or something, or whether it be a small operation- a family-run garage or shop, or whether it be the biggest corporation in Australia, whoever that is- if you're running a major mining operation. So, Codes of Practice provide minimum requirements. These are the things that you must comply with. In high-risk industries, you're probably going to have to do a lot more. And they do have a workplace application. So, they are written for the workplace. They're not really written for the designer, manufacturer, importer, supplier, etc. But nevertheless, it is very, very helpful if you are those people to look at the CoP in order to get an idea of what your customers have got to comply with and therefore what you're going to have to supply.
And as I've already said, CoP will repay careful reading because whilst they are guidance, they are really more than guidance. If you are ignorant of CoP and you don't do what they say you are exposing yourself to prosecution. So, see my introduction to Codes of Practice where I talk about that. There are three reasons why you must be aware of Codes of Practice. And this is one of those two Codes of Practice that everyone must be aware of. The others- if you're working with asbestos or welding or whatever it might be then there are specific Codes of Practice that you must be aware of for those activities. But this is one of those ones that applies to absolutely everybody, potentially. And as I've said before, the Model CoP has more detail than maybe some of the regulator-enforced Codes of Practice, which you will, I think, find helpful for higher risk applications. Whether legally you've got an MHF or not.
Commentary #2
And in fact, that's my point in slide two. So, not everyone is required to have a formal safety management system for managing safety risk in a- while something is in service, while it's being used. So, this CoP does not require us to have a formal safety management system, but it is required for major hazard facilities.
#AustralianWHS #CodesofPractice #Consult #Cooperate #Coordinate #coursesafetyengineering #engineersafety #ineedsafety #knowledgeofsafety #learnsafety #needforsafety #safetyblog #safetydo #safetyengineer #safetyengineerskills #safetyengineertraining #safetyengineeringcourse #safetyprinciples #softwaresafety #theneedforsafety #WHSCodeofPractice
Simon Di Nucci
https://www.safetyartisan.com/2020/11/21/consultation-cooperation-coordination-cop/
Monday, September 30, 2024
Monday, September 23, 2024
Risk Management Code of Practice
In this 40-minute session, we look at the Risk Management Code of Practice (CoP). We cover: who has WHS duties; the four-step process; keeping records, appendices & a summary of detailed requirements; and further commentary. This CoP is one of the two that are generally applicable.
https://youtu.be/9WFZrPVWIEU
The Risk Management Code of Practice (Demo of the full, 40-minute, video).
buy the full-length video here
Risk Management Code of Practice: Topics
Risk Management Code of Practice (CoP):
- Who has WHS duties;
- The four-step process;
- Keeping records, appendices & summary of detailed requirements;
- Further commentary; and
- Where to get more information.
Risk Management Code of Practice: Transcript
Risk Management Code of Practice: Transcript
Hello, everyone, and welcome to the Safety Artisan. I'm Simon, your host, and today we're going to be talking about the Risk Management Code of Practice.
Today we're talking about the Risk Management Code of Practice. It's a code of practice that I've used myself. I've used it to guide my work and to guide other people to help them in their work. I've used it to simplify the whole practice of what we do because once you know what you're supposed to do, you can do that and then you don't have to worry about working out what you need to do. And conversely, it's giving you everything you need to do so you can do more if you want to, but you don't have to. So, it makes life a lot easier and simpler. And then finally, you can use it to justify what you've done. That what you've done is correct, and what you've done is complete and is enough. So, it's very useful and that's why I'm teaching it because it makes life easier.
And I'm going to explain how to use it- you'll still need to go away and read the Code of Practice, as you'll see, to get all the details – but I'm going to go through the leading particulars and explain how to use it. And then finally, at the end of the session, I'm going to show you where you can get more help on this topic and indeed other related topics because this Code of Practice is one of several. And there's one other that you must refer to. This Risk Management Code of Practice is one that you really can't do without. There is one more and then the others are optional, depending on whether you're working in their respective areas. Anyway, let's get on with it.
Code of Practice: Risk Management
So we're talking about the Risk Management Code of Practice, which is under Australian Work Health and Safety Law. Now, if you're not operating in Australia, this is not a requirement for you but nevertheless, it does contain some very useful guidance. And I've seen similar requirements in the US and in the UK, and I suspect all across the English-speaking world.
Topics for this Session
So, what we're going to cover today. First of all, who has WHS duties because it's a wider group of people than you might think it is. There's the four-step process for actually doing risk management. And then I think we've got a slide each on keeping records, the appendices in the Code of Practice, and a summary of the detailed requirements in the Code of Practice. Then I’ve provided some further commentary and, as I’ve said before, where to get more information.
Who has WHS Duties?
So, first of all, who has WHS duties? Well, it's kind of everybody. First of all, if you are a person conducting a business or undertaking or a PCBU for short, then you have duties. And it says business or undertaking, so it includes voluntary groups, non-profit, government, military, you name it. It doesn't have to be a commercial business. Then you have duties if you are a designer, manufacturer, importer, supplier, or if you install test or commission plant substances or structures. So again, a wide range of people.
And it's not just about managing safety in a workplace. There're lots of duties on duty holders with upstream software- sorry not software, upstream safety duties. Like designers and manufacturers. Then finally, officers have additional duties and an officer basically is like a director of a company that sort of level. So, senior management with control over resources and they have to provide due diligence. So, there's a bunch of requirements on them as well. And then, of course, there's the workers and any visitors. They've got to cooperate and take reasonable care of themselves and look out for each other, which is all very important.
And as it says, and this is a quote from the CoP, “A person can have more than one duty at the same time, and more than one person can share the same duty”. So, you can't go playing tag, as it were. A sort of a responsibility tag. ‘It wasn't me. It was him. Governor!’ The court ultimately decides who is responsible.
A Four-Step Process
So, in our four-step process, we have; first of all, we have to identify hazards. We have to assess the risks. So, we need to look at causes and consequences. And the CoP doesn't say this, but exposure comes into it as well. So, a risk might be present, but if nobody is exposed to that risk, then you can't hurt them. So, that's an important point to remember. And controlling exposure is important to one degree or another in almost all areas, but very important in certain industries. Those industries that have got the real estate to be able to separate the risky thing from the human and this is very useful. So step three, we have to control risks. And then step four, we have to review control measures because it's recognized that these control measures will be in place for some time, for the lifetime of whatever it is we're doing or undertaking. So, they need to be periodically reviewed and there's guidance on that.
Now, I keep saying guidance – take a look at the introduction to Codes of Practice and you will see why Codes of Practice are a bit more than guidance. They are guidance that you cannot afford to ignore because if things go wrong, you will get hung out to dry based on what CoP said you should have done. So, if you are ignorant of what CoP said and haven't done it, then you're stuffed basically before you even start. That's point one to note.
And secondly, you'll notice in the diagram on the left, we've got management commitment at the centre and we've got consultation all the way around. And there's another Code of Practice, the Code of Practice on Communication, Cooperation and Coordination . So the C,C&C CoP and that is the other CoP that is essential. So, this one and the C, C and C CoP you must have a look at because they apply to everything in effect. Let's move on.
Step 1, Identify Hazards
So, first of all, we need to identify hazards. Now, CoP is written for any Australian business or undertaking, so it's pretty basic. It's pretty pragmatic, but it's pretty basic and it's got a workplace focus. So, it says inspect the workplace, look around, talk to your workers. Now, I work in a business and day job for a consultancy where we, generally speaking, are not looking at an existing workplace, but we're helping a customer buy or assure a complex product that's going to come into service at some time in the future. So, there are no current workers to discuss, but we always do try and include end-user representatives in our safety workshops. So, you may not be able to consult workers directly, but you should try and include people who have relevant work experience.
Secondly, the CoP tells us to use good work design and safe design. Now that's a whole topic in itself and I've got some guidance on safe design. If you go to that safety artisan.com page on safe design (www.safetyartisan.com/welcome/safe-design), you will see it and I'll take you through the subject and refer you on to the source material itself.
Thirdly, we need to consult supply chains and networks. I think that works two ways. First of all, when you get people to supply you stuff, make sure that they supply the data that you need. The safety data, all the information that you need to take and use the product safely. And that's part of the duty on all of these duty holders, on the designer, the manufacturer, the importer, the supplier. They all have duties to pass on the relevant safety information but make sure you ask for it in your contract. And secondly, suppliers, particularly if you're buying an expensive piece of kit off them, suppliers can be an excellent source of information. If they're the designers, then they know this kit better than anybody else. Make use of their expertise, contract them to do some work for you and take part of the load off you. They are best placed to do some of the work, so get them to do it.
And then fourthly, it says review available information. Now, this is very important. There's historical information or there should be – it’s not always easy to come by sometimes. Do make the effort to get actual historical information for your piece of kit, maybe from the supplier. Or if you can't do that, if it's a new piece of kit, then try and get information on similar equipment, or services, or functionality, or go to a trade organization, or go to the regulator depending on what domain you're in. Do look around for historical information. It is out there. It can be hard to find, but it is worth the effort because, again, the guidance requires it. So, if you don't do it, if you don't bother or you've not made reasonable efforts to do so, you'll get clobbered if things go wrong.
And then it's also advisable to compliment that historical information with diverse approaches. One of them is you can use a hazard checklist approach, and we talk about that in the session on preliminary hazard identification. There are lots of checklists freely available out there on the Internet. Some are general and some are more specific to different pieces of kit or different domains. Try and find the most relevant one for you and use it. And then maybe there are specific safety analyses techniques that you can use as well so have a go at those. And a lot of them are quite simple so don't be put off. You don't have to necessarily have to get an expensive consultant in to do this for you. A lot of these techniques are really quite simple and just require a bit of imagination and a little bit of self-discipline in the way you go about it. And I talk about analysis methods for hazard identification in that same session on Preliminary Hazard Identification (PHI).
So, that's identifying hazards.
Step 2, Assess Risks
Step two, we need to assess the risks. So, if we recall risk is a combination of likelihood and severity. So, how likely is the harm could arise? And how severe is that harm? The way to do that, the CoP says, is to work out how hazards may cause harm. And as always, don't be afraid to ask the dumb questions. That's part of my job as a consultant. You're allowed to turn up and ask dumb questions. Or maybe sensitive questions that nobody in the firm dares to ask because they think they get fired. So, be brave and do try and work out how to ask the questions in a non-threatening way, but do ask the questions.
Work out how severe the harm could be. What is the worst credible consequence? And also, to keep it simple, what's the worst direct consequence? Yes, you can come up with a fanciful chain of events that will lead to ‘it's the end of the world as we know it’, but keep it direct would be my advice. At least to start with. It's better to get a range of stuff than to work one scenario to the nth degree, I would suggest.
Then work out the likelihood of that harm occurring. Very often the most severe harm can only occur when there is a particular combination of circumstances. And if you read any kind of accident report, even in the press, you'll very often say this was happening and it just so happened on this particular day that somebody wasn't available to supervise and then this went wrong and something else went wrong. And then the final result of this chain of consequences was somebody gets hurt. So, do factor in all of those things.
There are probably lots of existing controls already unless you're doing something very novel indeed, which is unusual. So, do look at what's there and record it all. Conversely, do be aware of the ‘it will never happen brigade’ is I've met several people who say, ‘Oh, that will never happen; or was it ‘No British pilot would be stupid enough to do that. Ho, ho, ho.’ I was foolish enough to believe that. Anyway, that's another story. So, don't believe the people who say, ‘It can never happen’. Well, if I say, ‘OK, what's the justification? Why can it never happen? Where's the evidence for that claim?’ So, do dig into those responses.
There's more detail in the Code of Practice. There are some good questions to ask in the workplace. And with a bit of imagination, you can take your imaginary piece of kit and sort of think about it in the workplace and go, ‘Well, let's think up a suitable question.’ So, there's good guidance in there. Historical data can't be beat as a reality check and it shuts up the naysayers as well because if you can pull out information, say, ‘Well this accident has happened and it's happened lots of times to lots of good people who thought they were clever’. So, it shuts up the naysayers do work hard to get the historical data. It's fantastic if you can get it.
And then, as I said before, there are multiple specialist cause and consequence analysis techniques available. I talk about some of them and in other posts that I've already done, and I will talk about more in the future. But you may not need that level of sophistication. It's always better to do some good basic work as early as you can. Then maybe if you come up against something and say, ‘We're not cracking this. We suspect there's a problem, but we can't be sure’ then think about bringing out big guns. But if you've done the basic work first, that will really help you zero in on the areas where you think you need to do more work.
Step 3, Control Risks
The third one, controlling risks. Really, this is what it's all about because you can do all the analysis you like, but you don't do analysis for the sake of it. You do analysis in order to inform your selection of risk controls. And we are required to use a hierarchy of control measures, and that's a legal requirement in Australia. It's also a requirement in other jurisdictions and in other many other standards – safety standards that you'll see it just may not be called this. But it will talk about more and less effective controls.
At the top of the control hierarchy, we've got the most effective control which is to eliminate the risk entirely. And by that, I mean you get rid of it. Let's say you're working in an explosive atmosphere and you've decided you don't want any electrical devices in that explosive atmosphere. So, if you need to have power for machinery, you're going to do it with pneumatics, let's say, or hydraulics. So, you've eliminated the electrical risk. Elimination does not mean massaging the probability figures to get them very low and then you have eliminated the risk you have not. You've just played games with probability figures. So first off, that's what elimination really means.
The second level, you've got three choices. We can substitute something hazardous with a safer alternative. I've mentioned getting rid of electricity entirely. You could say, ‘Well, I've got hydraulics, but they can burst and cause damage so I'll have something else. Or let's say there was a particular lubricant, which is ideal, but actually it's quite dangerous this lubricant, so we'll pick something safer. Maybe it doesn't perform quite as well. Or a refrigerant, let's say, an ideal refrigerant might be a potent greenhouse gas so we go ‘We're going to have something else instead’.
You can isolate the hazard from people – I've spoken about that before. Some industries you've got a lot of real estate to play with. You can keep the hazard away from people. Or you can reduce the risk through engineering controls. And by engineering controls, I mean, you can build a safety feature or an interlock or something physically into the product. You're not relying on a person to avoid the risk. It's been done for them. It's automatic or built-in.
At third level, we can use admin controls. So we can give people procedures and rules and we can say, ‘Do this, don't do that’. And most of the time they'll probably do it and obey the rules, but sometimes they won't. And sometimes for good reason, by the way, because people come up with ridiculous rules that can't be obeyed or that make the task or the job so difficult that people break the rules all the time because that's the only way to get the job done effectively. So, do be aware of putting silly controls onto people because they won't get obeyed. It's your responsibility to consult the workers and come up with something practical.
And then finally, we can use personal protective equipment. Now that doesn't do anything to the probability of the accident, but it reduces the severity. So, for example, if I'm wearing a hard hat, something falls on my head. It reduces the severity of the accident. If I'm wearing protective goggles and there's a spark or a piece of debris flies out of the machine. If I'm wearing the goggles, it just bounces off probably and saves my eyes. So, there's a couple of really good examples of where the PPE will help us. And of course, in this season of COVID, we've all got PPE bonkers. It's become headline news all over the world. So, we all now know what PPE is, which is great. Well, and it's not great. It's terrible, but it's good for knowledge.
So, we have to work through that hierarchy in that order. We have to see whether it's feasible to eliminate the risk to start at the top with the most effective controls and work our way down. We have to do that. And the subject of another chat, another lesson, we have to apply all reasonably practical controls in order to say that we have eliminated or minimized risks SFARP. So far as is reasonably practicable. So, we've got to apply all reasonably practical controls. I'll explain exactly what that means in a separate session.
Aside: Control Effectiveness
A Quick aside: are controls effective? I've sort of hinted at this before about the admin stuff. How do we get effective controls? Well, the CoP says we need people to be accountable for health and safety. We need maintenance of plant and equipment. We need up to date training and competency for our people. We need up to date hazard information – that's a duty in its own right. And we need regular review and consultation. And you'll find out about that in the CC&C CoP in my next lesson.
Now, these things are required everywhere, they can be achieved informally. If you work in a high-risk industry, you'll probably have a thing called a safety management system. And your safety management system will be documented in a safety management plan. And typically, the safety management system is the thing that delivers all of these things, all five of these things and much more. So, that's what you'll probably end up doing.
First thing to say on that, of course, is that this information has got to be generated. You've got to get it from source and it's usually the designer, the manufacturer, and the installer, and the testers who can provide this information. So, do make sure that you are imposing requirements on your suppliers, on your subcontractors to do this stuff and to provide you with the information. It is their duty to do so. It's a legal duty, but you're probably still going to have to pay for it and say when you want it and in what format that's most useful to you and all the other good stuff.
Step 4, Reviewing Controls
Step four, which is maybe not so obvious. We've got some controls, we're up and running, we need to review those controls.
#coursesafetyengineering #engineersafety #ineedsafety #knowledgeofsafety #learnsafety #needforsafety #riskanalysis #riskassessment #riskmanagement #safetyblog #safetydo #safetyengineer #safetyengineerskills #safetyengineertraining #safetyengineeringcourse #safetyprinciples #softwaresafety #theneedforsafety #WHSCodeofPractice
Simon Di Nucci
https://www.safetyartisan.com/2020/10/19/risk-management-code-of-practice/
In this 40-minute session, we look at the Risk Management Code of Practice (CoP). We cover: who has WHS duties; the four-step process; keeping records, appendices & a summary of detailed requirements; and further commentary. This CoP is one of the two that are generally applicable.
https://youtu.be/9WFZrPVWIEU
The Risk Management Code of Practice (Demo of the full, 40-minute, video).
buy the full-length video here
Risk Management Code of Practice: Topics
Risk Management Code of Practice (CoP):
- Who has WHS duties;
- The four-step process;
- Keeping records, appendices & summary of detailed requirements;
- Further commentary; and
- Where to get more information.
Risk Management Code of Practice: Transcript
Risk Management Code of Practice: Transcript
Hello, everyone, and welcome to the Safety Artisan. I'm Simon, your host, and today we're going to be talking about the Risk Management Code of Practice.
Today we're talking about the Risk Management Code of Practice. It's a code of practice that I've used myself. I've used it to guide my work and to guide other people to help them in their work. I've used it to simplify the whole practice of what we do because once you know what you're supposed to do, you can do that and then you don't have to worry about working out what you need to do. And conversely, it's giving you everything you need to do so you can do more if you want to, but you don't have to. So, it makes life a lot easier and simpler. And then finally, you can use it to justify what you've done. That what you've done is correct, and what you've done is complete and is enough. So, it's very useful and that's why I'm teaching it because it makes life easier.
And I'm going to explain how to use it- you'll still need to go away and read the Code of Practice, as you'll see, to get all the details – but I'm going to go through the leading particulars and explain how to use it. And then finally, at the end of the session, I'm going to show you where you can get more help on this topic and indeed other related topics because this Code of Practice is one of several. And there's one other that you must refer to. This Risk Management Code of Practice is one that you really can't do without. There is one more and then the others are optional, depending on whether you're working in their respective areas. Anyway, let's get on with it.
Code of Practice: Risk Management
So we're talking about the Risk Management Code of Practice, which is under Australian Work Health and Safety Law. Now, if you're not operating in Australia, this is not a requirement for you but nevertheless, it does contain some very useful guidance. And I've seen similar requirements in the US and in the UK, and I suspect all across the English-speaking world.
Topics for this Session
So, what we're going to cover today. First of all, who has WHS duties because it's a wider group of people than you might think it is. There's the four-step process for actually doing risk management. And then I think we've got a slide each on keeping records, the appendices in the Code of Practice, and a summary of the detailed requirements in the Code of Practice. Then I’ve provided some further commentary and, as I’ve said before, where to get more information.
Who has WHS Duties?
So, first of all, who has WHS duties? Well, it's kind of everybody. First of all, if you are a person conducting a business or undertaking or a PCBU for short, then you have duties. And it says business or undertaking, so it includes voluntary groups, non-profit, government, military, you name it. It doesn't have to be a commercial business. Then you have duties if you are a designer, manufacturer, importer, supplier, or if you install test or commission plant substances or structures. So again, a wide range of people.
And it's not just about managing safety in a workplace. There're lots of duties on duty holders with upstream software- sorry not software, upstream safety duties. Like designers and manufacturers. Then finally, officers have additional duties and an officer basically is like a director of a company that sort of level. So, senior management with control over resources and they have to provide due diligence. So, there's a bunch of requirements on them as well. And then, of course, there's the workers and any visitors. They've got to cooperate and take reasonable care of themselves and look out for each other, which is all very important.
And as it says, and this is a quote from the CoP, “A person can have more than one duty at the same time, and more than one person can share the same duty”. So, you can't go playing tag, as it were. A sort of a responsibility tag. ‘It wasn't me. It was him. Governor!’ The court ultimately decides who is responsible.
A Four-Step Process
So, in our four-step process, we have; first of all, we have to identify hazards. We have to assess the risks. So, we need to look at causes and consequences. And the CoP doesn't say this, but exposure comes into it as well. So, a risk might be present, but if nobody is exposed to that risk, then you can't hurt them. So, that's an important point to remember. And controlling exposure is important to one degree or another in almost all areas, but very important in certain industries. Those industries that have got the real estate to be able to separate the risky thing from the human and this is very useful. So step three, we have to control risks. And then step four, we have to review control measures because it's recognized that these control measures will be in place for some time, for the lifetime of whatever it is we're doing or undertaking. So, they need to be periodically reviewed and there's guidance on that.
Now, I keep saying guidance – take a look at the introduction to Codes of Practice and you will see why Codes of Practice are a bit more than guidance. They are guidance that you cannot afford to ignore because if things go wrong, you will get hung out to dry based on what CoP said you should have done. So, if you are ignorant of what CoP said and haven't done it, then you're stuffed basically before you even start. That's point one to note.
And secondly, you'll notice in the diagram on the left, we've got management commitment at the centre and we've got consultation all the way around. And there's another Code of Practice, the Code of Practice on Communication, Cooperation and Coordination . So the C,C&C CoP and that is the other CoP that is essential. So, this one and the C, C and C CoP you must have a look at because they apply to everything in effect. Let's move on.
Step 1, Identify Hazards
So, first of all, we need to identify hazards. Now, CoP is written for any Australian business or undertaking, so it's pretty basic. It's pretty pragmatic, but it's pretty basic and it's got a workplace focus. So, it says inspect the workplace, look around, talk to your workers. Now, I work in a business and day job for a consultancy where we, generally speaking, are not looking at an existing workplace, but we're helping a customer buy or assure a complex product that's going to come into service at some time in the future. So, there are no current workers to discuss, but we always do try and include end-user representatives in our safety workshops. So, you may not be able to consult workers directly, but you should try and include people who have relevant work experience.
Secondly, the CoP tells us to use good work design and safe design. Now that's a whole topic in itself and I've got some guidance on safe design. If you go to that safety artisan.com page on safe design (www.safetyartisan.com/welcome/safe-design), you will see it and I'll take you through the subject and refer you on to the source material itself.
Thirdly, we need to consult supply chains and networks. I think that works two ways. First of all, when you get people to supply you stuff, make sure that they supply the data that you need. The safety data, all the information that you need to take and use the product safely. And that's part of the duty on all of these duty holders, on the designer, the manufacturer, the importer, the supplier. They all have duties to pass on the relevant safety information but make sure you ask for it in your contract. And secondly, suppliers, particularly if you're buying an expensive piece of kit off them, suppliers can be an excellent source of information. If they're the designers, then they know this kit better than anybody else. Make use of their expertise, contract them to do some work for you and take part of the load off you. They are best placed to do some of the work, so get them to do it.
And then fourthly, it says review available information. Now, this is very important. There's historical information or there should be – it’s not always easy to come by sometimes. Do make the effort to get actual historical information for your piece of kit, maybe from the supplier. Or if you can't do that, if it's a new piece of kit, then try and get information on similar equipment, or services, or functionality, or go to a trade organization, or go to the regulator depending on what domain you're in. Do look around for historical information. It is out there. It can be hard to find, but it is worth the effort because, again, the guidance requires it. So, if you don't do it, if you don't bother or you've not made reasonable efforts to do so, you'll get clobbered if things go wrong.
And then it's also advisable to compliment that historical information with diverse approaches. One of them is you can use a hazard checklist approach, and we talk about that in the session on preliminary hazard identification. There are lots of checklists freely available out there on the Internet. Some are general and some are more specific to different pieces of kit or different domains. Try and find the most relevant one for you and use it. And then maybe there are specific safety analyses techniques that you can use as well so have a go at those. And a lot of them are quite simple so don't be put off. You don't have to necessarily have to get an expensive consultant in to do this for you. A lot of these techniques are really quite simple and just require a bit of imagination and a little bit of self-discipline in the way you go about it. And I talk about analysis methods for hazard identification in that same session on Preliminary Hazard Identification (PHI).
So, that's identifying hazards.
Step 2, Assess Risks
Step two, we need to assess the risks. So, if we recall risk is a combination of likelihood and severity. So, how likely is the harm could arise? And how severe is that harm? The way to do that, the CoP says, is to work out how hazards may cause harm. And as always, don't be afraid to ask the dumb questions. That's part of my job as a consultant. You're allowed to turn up and ask dumb questions. Or maybe sensitive questions that nobody in the firm dares to ask because they think they get fired. So, be brave and do try and work out how to ask the questions in a non-threatening way, but do ask the questions.
Work out how severe the harm could be. What is the worst credible consequence? And also, to keep it simple, what's the worst direct consequence? Yes, you can come up with a fanciful chain of events that will lead to ‘it's the end of the world as we know it’, but keep it direct would be my advice. At least to start with. It's better to get a range of stuff than to work one scenario to the nth degree, I would suggest.
Then work out the likelihood of that harm occurring. Very often the most severe harm can only occur when there is a particular combination of circumstances. And if you read any kind of accident report, even in the press, you'll very often say this was happening and it just so happened on this particular day that somebody wasn't available to supervise and then this went wrong and something else went wrong. And then the final result of this chain of consequences was somebody gets hurt. So, do factor in all of those things.
There are probably lots of existing controls already unless you're doing something very novel indeed, which is unusual. So, do look at what's there and record it all. Conversely, do be aware of the ‘it will never happen brigade’ is I've met several people who say, ‘Oh, that will never happen; or was it ‘No British pilot would be stupid enough to do that. Ho, ho, ho.’ I was foolish enough to believe that. Anyway, that's another story. So, don't believe the people who say, ‘It can never happen’. Well, if I say, ‘OK, what's the justification? Why can it never happen? Where's the evidence for that claim?’ So, do dig into those responses.
There's more detail in the Code of Practice. There are some good questions to ask in the workplace. And with a bit of imagination, you can take your imaginary piece of kit and sort of think about it in the workplace and go, ‘Well, let's think up a suitable question.’ So, there's good guidance in there. Historical data can't be beat as a reality check and it shuts up the naysayers as well because if you can pull out information, say, ‘Well this accident has happened and it's happened lots of times to lots of good people who thought they were clever’. So, it shuts up the naysayers do work hard to get the historical data. It's fantastic if you can get it.
And then, as I said before, there are multiple specialist cause and consequence analysis techniques available. I talk about some of them and in other posts that I've already done, and I will talk about more in the future. But you may not need that level of sophistication. It's always better to do some good basic work as early as you can. Then maybe if you come up against something and say, ‘We're not cracking this. We suspect there's a problem, but we can't be sure’ then think about bringing out big guns. But if you've done the basic work first, that will really help you zero in on the areas where you think you need to do more work.
Step 3, Control Risks
The third one, controlling risks. Really, this is what it's all about because you can do all the analysis you like, but you don't do analysis for the sake of it. You do analysis in order to inform your selection of risk controls. And we are required to use a hierarchy of control measures, and that's a legal requirement in Australia. It's also a requirement in other jurisdictions and in other many other standards – safety standards that you'll see it just may not be called this. But it will talk about more and less effective controls.
At the top of the control hierarchy, we've got the most effective control which is to eliminate the risk entirely. And by that, I mean you get rid of it. Let's say you're working in an explosive atmosphere and you've decided you don't want any electrical devices in that explosive atmosphere. So, if you need to have power for machinery, you're going to do it with pneumatics, let's say, or hydraulics. So, you've eliminated the electrical risk. Elimination does not mean massaging the probability figures to get them very low and then you have eliminated the risk you have not. You've just played games with probability figures. So first off, that's what elimination really means.
The second level, you've got three choices. We can substitute something hazardous with a safer alternative. I've mentioned getting rid of electricity entirely. You could say, ‘Well, I've got hydraulics, but they can burst and cause damage so I'll have something else. Or let's say there was a particular lubricant, which is ideal, but actually it's quite dangerous this lubricant, so we'll pick something safer. Maybe it doesn't perform quite as well. Or a refrigerant, let's say, an ideal refrigerant might be a potent greenhouse gas so we go ‘We're going to have something else instead’.
You can isolate the hazard from people – I've spoken about that before. Some industries you've got a lot of real estate to play with. You can keep the hazard away from people. Or you can reduce the risk through engineering controls. And by engineering controls, I mean, you can build a safety feature or an interlock or something physically into the product. You're not relying on a person to avoid the risk. It's been done for them. It's automatic or built-in.
At third level, we can use admin controls. So we can give people procedures and rules and we can say, ‘Do this, don't do that’. And most of the time they'll probably do it and obey the rules, but sometimes they won't. And sometimes for good reason, by the way, because people come up with ridiculous rules that can't be obeyed or that make the task or the job so difficult that people break the rules all the time because that's the only way to get the job done effectively. So, do be aware of putting silly controls onto people because they won't get obeyed. It's your responsibility to consult the workers and come up with something practical.
And then finally, we can use personal protective equipment. Now that doesn't do anything to the probability of the accident, but it reduces the severity. So, for example, if I'm wearing a hard hat, something falls on my head. It reduces the severity of the accident. If I'm wearing protective goggles and there's a spark or a piece of debris flies out of the machine. If I'm wearing the goggles, it just bounces off probably and saves my eyes. So, there's a couple of really good examples of where the PPE will help us. And of course, in this season of COVID, we've all got PPE bonkers. It's become headline news all over the world. So, we all now know what PPE is, which is great. Well, and it's not great. It's terrible, but it's good for knowledge.
So, we have to work through that hierarchy in that order. We have to see whether it's feasible to eliminate the risk to start at the top with the most effective controls and work our way down. We have to do that. And the subject of another chat, another lesson, we have to apply all reasonably practical controls in order to say that we have eliminated or minimized risks SFARP. So far as is reasonably practicable. So, we've got to apply all reasonably practical controls. I'll explain exactly what that means in a separate session.
Aside: Control Effectiveness
A Quick aside: are controls effective? I've sort of hinted at this before about the admin stuff. How do we get effective controls? Well, the CoP says we need people to be accountable for health and safety. We need maintenance of plant and equipment. We need up to date training and competency for our people. We need up to date hazard information – that's a duty in its own right. And we need regular review and consultation. And you'll find out about that in the CC&C CoP in my next lesson.
Now, these things are required everywhere, they can be achieved informally. If you work in a high-risk industry, you'll probably have a thing called a safety management system. And your safety management system will be documented in a safety management plan. And typically, the safety management system is the thing that delivers all of these things, all five of these things and much more. So, that's what you'll probably end up doing.
First thing to say on that, of course, is that this information has got to be generated. You've got to get it from source and it's usually the designer, the manufacturer, and the installer, and the testers who can provide this information. So, do make sure that you are imposing requirements on your suppliers, on your subcontractors to do this stuff and to provide you with the information. It is their duty to do so. It's a legal duty, but you're probably still going to have to pay for it and say when you want it and in what format that's most useful to you and all the other good stuff.
Step 4, Reviewing Controls
Step four, which is maybe not so obvious. We've got some controls, we're up and running, we need to review those controls.
#coursesafetyengineering #engineersafety #ineedsafety #knowledgeofsafety #learnsafety #needforsafety #riskanalysis #riskassessment #riskmanagement #safetyblog #safetydo #safetyengineer #safetyengineerskills #safetyengineertraining #safetyengineeringcourse #safetyprinciples #softwaresafety #theneedforsafety #WHSCodeofPractice
Simon Di Nucci
https://www.safetyartisan.com/2020/10/19/risk-management-code-of-practice/
Monday, September 16, 2024
Connect
Connect with the Safety Artisan - get the latest information and tell us what you need to know!
Join Our Email List
Sign up for our newsletter to get monthly updates on what's coming next and where to find it. Subscribers get a FREE course - learn how to combine different safety analyses into a Program.
This is the Website of The Safety Artisan Pty Ltd, ABN: 36677589730. You can find our Terms of Use, Privacy Policy, and Conditions of Sale below.
sign up
Never Miss Another Video
Subscribe to the Safety Artisan Channel on YouTube, and get notified every time a new video comes out.
Subscribe
Connect with us on Social Media
Connect: Get Support
Browse with Confidence
By continuing to use this website, you agree to these Website Terms of Use and Disclaimer:
- Notice to visitors browsing this website:
- You must only use it for lawful purposes;
- You must not post defamatory or offensive material, harass or cause distress to any person or disrupt the website;
- You must not change, remove, deface, hack or otherwise interfere with this website; and
- I reserve right to ban persons from using this website.
- Simon Di Nucci asserts his right to:
- Ownership of copyright of website materials (material owned by other parties is acknowledged and used in accordance with the applicable rules); and
- Ownership of The Safety Artisan Business Name and Logo.
- Visitors are granted a license to use this website and print pages for personal and non-commercial use.
- Exclusions of liability:
- Links to other websites do not necessarily endorse or support information on those websites – you use them at your own risk.
- Liability for loss or damage resulting from errors, interruptions, defects, delays, malware/viruses, lost or stolen or misused data, unlawful third-party conduct arising out of the website is excluded.
- Liability for negligence is excluded.
- Liability for financial loss (i.e. special, indirect and consequential loss) is excluded.
- You agree to indemnify and hold The Safety Artisan, its officers, directors, shareholders, predecessors, successors in interest, employees, agents, subsidiaries and affiliates, harmless from any demands, loss, liability, claims or expenses (including legal fees), made against The Safety Artisan by any third party due to or arising out of or in connection with your use of this website.
- This website is governed by the law of South Australia.
Connect with Confidence
Privacy Policy:
- This website collects and stores cookies, in compliance with GPDR and CCPA legislation, and only in accordance with the permission you give in the pop-up banner.
- If you subscribe to my email list, it will collect your name and email address (using a GPDR-compliant form).
- The website collects, holds and uses cookies to enhance your browsing experience and monitor website performance.
- Your email list personal information is collected and securely stored by MailChimp - not on this website.
- I will not ‘spam’ you, nor sell or rent any visitor’s email address.
- You may request the information that I store on you by email (see below) and ask me to correct any errors.
- You can unsubscribe from my email list at any time by clicking on the link at the bottom of every email.
- You can notify me of any breach of the Australian Privacy Principles by email - I will deal with your complaint as quickly as I can.
- I don't disclose personal information to other people or organisations, except for MailChimp, which is based in the USA.
- Use the feedback form (above) or email me: admin@safetyartisan.com
Conditions of Sale
Conditions of Sale:
- These Conditions of Sale should be read in conjunction with the website Terms of Use.
- There is a legally binding agreement to the sale when an order is confirmed.
- If there is a pricing error, we may choose not to fill the order and issue a refund.
- Payment terms – for payment method, e.g. Paypal or credit cards, we are not liable for loss or damage as a result of the use of third party-gateway provider facilities.
- We deliver goods to you by use of a third-party delivery company (Easy Digital Downloads).
- You get access to and use of online products and services through our website.
- You download video lessons via the link that we provide to you – ten (10) attempts are permitted.
- You cannot create an online account with us and we do not store your credit card details.
- We do give refunds unless we are unable to supply an item.
- We confirm ownership of the copyright in services (video lessons) and website content.
- Nothing in these Conditions of Sale excludes liability for breach of consumer guarantees under Australian Consumer Law (ACL).
- You accept these Conditions of Sale by clicking on the “I agree” box before proceeding to purchase.
The Safety Artisan will not sell your Personal Information
Who is the Safety Artisan? Find out here.
Simon Di Nucci
https://www.safetyartisan.com/connect/
Connect with the Safety Artisan - get the latest information and tell us what you need to know!
Join Our Email List
Sign up for our newsletter to get monthly updates on what's coming next and where to find it. Subscribers get a FREE course - learn how to combine different safety analyses into a Program.
This is the Website of The Safety Artisan Pty Ltd, ABN: 36677589730. You can find our Terms of Use, Privacy Policy, and Conditions of Sale below.
sign up
Never Miss Another Video
Subscribe to the Safety Artisan Channel on YouTube, and get notified every time a new video comes out.
Subscribe
Connect with us on Social Media
Connect: Get Support
Browse with Confidence
By continuing to use this website, you agree to these Website Terms of Use and Disclaimer:
- Notice to visitors browsing this website:
- You must only use it for lawful purposes;
- You must not post defamatory or offensive material, harass or cause distress to any person or disrupt the website;
- You must not change, remove, deface, hack or otherwise interfere with this website; and
- I reserve right to ban persons from using this website.
- Simon Di Nucci asserts his right to:
- Ownership of copyright of website materials (material owned by other parties is acknowledged and used in accordance with the applicable rules); and
- Ownership of The Safety Artisan Business Name and Logo.
- Visitors are granted a license to use this website and print pages for personal and non-commercial use.
- Exclusions of liability:
- Links to other websites do not necessarily endorse or support information on those websites – you use them at your own risk.
- Liability for loss or damage resulting from errors, interruptions, defects, delays, malware/viruses, lost or stolen or misused data, unlawful third-party conduct arising out of the website is excluded.
- Liability for negligence is excluded.
- Liability for financial loss (i.e. special, indirect and consequential loss) is excluded.
- You agree to indemnify and hold The Safety Artisan, its officers, directors, shareholders, predecessors, successors in interest, employees, agents, subsidiaries and affiliates, harmless from any demands, loss, liability, claims or expenses (including legal fees), made against The Safety Artisan by any third party due to or arising out of or in connection with your use of this website.
- This website is governed by the law of South Australia.
Connect with Confidence
Privacy Policy:
- This website collects and stores cookies, in compliance with GPDR and CCPA legislation, and only in accordance with the permission you give in the pop-up banner.
- If you subscribe to my email list, it will collect your name and email address (using a GPDR-compliant form).
- The website collects, holds and uses cookies to enhance your browsing experience and monitor website performance.
- Your email list personal information is collected and securely stored by MailChimp - not on this website.
- I will not ‘spam’ you, nor sell or rent any visitor’s email address.
- You may request the information that I store on you by email (see below) and ask me to correct any errors.
- You can unsubscribe from my email list at any time by clicking on the link at the bottom of every email.
- You can notify me of any breach of the Australian Privacy Principles by email - I will deal with your complaint as quickly as I can.
- I don't disclose personal information to other people or organisations, except for MailChimp, which is based in the USA.
- Use the feedback form (above) or email me: admin@safetyartisan.com
Conditions of Sale
Conditions of Sale:
- These Conditions of Sale should be read in conjunction with the website Terms of Use.
- There is a legally binding agreement to the sale when an order is confirmed.
- If there is a pricing error, we may choose not to fill the order and issue a refund.
- Payment terms – for payment method, e.g. Paypal or credit cards, we are not liable for loss or damage as a result of the use of third party-gateway provider facilities.
- We deliver goods to you by use of a third-party delivery company (Easy Digital Downloads).
- You get access to and use of online products and services through our website.
- You download video lessons via the link that we provide to you – ten (10) attempts are permitted.
- You cannot create an online account with us and we do not store your credit card details.
- We do give refunds unless we are unable to supply an item.
- We confirm ownership of the copyright in services (video lessons) and website content.
- Nothing in these Conditions of Sale excludes liability for breach of consumer guarantees under Australian Consumer Law (ACL).
- You accept these Conditions of Sale by clicking on the “I agree” box before proceeding to purchase.
The Safety Artisan will not sell your Personal Information
Who is the Safety Artisan? Find out here.
Simon Di Nucci
https://www.safetyartisan.com/connect/
Monday, September 9, 2024
About
About The Safety Artisan - Safety Engineering and Risk Management Expert
About The Safety Artisan
https://youtu.be/qebeBeGj__4
Hi, everyone, and welcome to The Safety Artisan. I'm Simon, and I just wanted to share with you briefly why I started this enterprise. I've had a career in safety, engineering, and safety consulting for over 25 years now. And in that time, I've seen customers make one of two mistakes quite often. First of all, I've seen customers not do some things that they should have been doing. This was usually because they just were ignorant of what their legal obligations were.
And I guess that's a fairly obvious mistake. That's what you would expect me to say. But more often, I've seen customers do too much to try and achieve safety, which is surprising! I've seen people waste a lot of time, energy, and money doing things that just didn't make a difference. Sometimes it actually got in the way of doing good safety work.
And I think the reasons for those mistakes are, first of all, ignorance.
Secondly, not knowing precisely what safety is and therefore not being able to work out how to get there. That's why I started The Safety Artisan. I wanted to equip people with the knowledge of what safety really is and the tools to get there efficiently. To neither do too much nor too little. We want Safety, Just Right.
Simon Di Nucci, CPEng, FIEAust, NERNational Engineering RegisterMy Certified Skills
I have 25+ years of experience in safety engineering and consultancy. I've worked on aircraft, ships, submarines, air-traffic management systems, trains, and software. As an engineer and consultant, I've served on tiny projects and some of the biggest programs in the world.
I have worked in the UK and Australia, and on several projects, I've introduced American-made systems to both countries. It has been my privilege to teach safety to hundreds of people in the classroom. And I've presented on safety topics at several international conferences. See my full resume/CV here.
Our Mission and Values
artisan/ˈɑːtɪzan,ɑːtɪˈzan/Learn to pronounce noun
A worker in a skilled trade, especially one that involves making things by hand. “street markets where local artisans display handwoven textiles, painted ceramics, and leather goods”.
When I was choosing a name for my business, I thought of quite a lot of alternatives. I settled on The Safety Artisan for three reasons. First, I liked the meaning of the word. An individual pursuing their craft and trying to do it to the very best of their abilities.
Second, I liked the application. I’ve worked on a lot of very large, even multi-billion-dollar projects; but we’re still knowledge workers. We’re still individuals who must be competent to deliver good results for people.
And third, I liked the idea. Imagine a cottage industry of artisans working at home, delivering goods and services that other people can use wherever they are. Right now, you might be home or you might be on your mobile phone listening to this.
So, I liked all three of those things. I thought, yes, that’s what I’m about. That’s what I believe in and want to do. Does that sound good to you, too? Then check out The Safety Artisan's Topics, where I provide #safety #engineering #training.
Simon Di Nucci
https://www.safetyartisan.com/about/
About The Safety Artisan - Safety Engineering and Risk Management Expert
About The Safety Artisan
https://youtu.be/qebeBeGj__4
Hi, everyone, and welcome to The Safety Artisan. I'm Simon, and I just wanted to share with you briefly why I started this enterprise. I've had a career in safety, engineering, and safety consulting for over 25 years now. And in that time, I've seen customers make one of two mistakes quite often. First of all, I've seen customers not do some things that they should have been doing. This was usually because they just were ignorant of what their legal obligations were.
And I guess that's a fairly obvious mistake. That's what you would expect me to say. But more often, I've seen customers do too much to try and achieve safety, which is surprising! I've seen people waste a lot of time, energy, and money doing things that just didn't make a difference. Sometimes it actually got in the way of doing good safety work.
And I think the reasons for those mistakes are, first of all, ignorance.
Secondly, not knowing precisely what safety is and therefore not being able to work out how to get there. That's why I started The Safety Artisan. I wanted to equip people with the knowledge of what safety really is and the tools to get there efficiently. To neither do too much nor too little. We want Safety, Just Right.
Simon Di Nucci, CPEng, FIEAust, NERNational Engineering RegisterMy Certified Skills
I have 25+ years of experience in safety engineering and consultancy. I've worked on aircraft, ships, submarines, air-traffic management systems, trains, and software. As an engineer and consultant, I've served on tiny projects and some of the biggest programs in the world.
I have worked in the UK and Australia, and on several projects, I've introduced American-made systems to both countries. It has been my privilege to teach safety to hundreds of people in the classroom. And I've presented on safety topics at several international conferences. See my full resume/CV here.
Our Mission and Values
artisan/ˈɑːtɪzan,ɑːtɪˈzan/Learn to pronounce noun
A worker in a skilled trade, especially one that involves making things by hand. “street markets where local artisans display handwoven textiles, painted ceramics, and leather goods”.
When I was choosing a name for my business, I thought of quite a lot of alternatives. I settled on The Safety Artisan for three reasons. First, I liked the meaning of the word. An individual pursuing their craft and trying to do it to the very best of their abilities.
Second, I liked the application. I’ve worked on a lot of very large, even multi-billion-dollar projects; but we’re still knowledge workers. We’re still individuals who must be competent to deliver good results for people.
And third, I liked the idea. Imagine a cottage industry of artisans working at home, delivering goods and services that other people can use wherever they are. Right now, you might be home or you might be on your mobile phone listening to this.
So, I liked all three of those things. I thought, yes, that’s what I’m about. That’s what I believe in and want to do. Does that sound good to you, too? Then check out The Safety Artisan's Topics, where I provide #safety #engineering #training.
Simon Di Nucci
https://www.safetyartisan.com/about/
Monday, September 2, 2024
Topics
Here are the main topics taught by The Safety Artisan. Each page will take you to several teaching videos and other resources. Go to the Connect page to see how you can get updates every time a video or resource is added.
Start Here
Start here if you are new to safety! The posts featured on this page introduce basic safety topics, such as definitions and fundamental safety concepts. You can also start here if you know how to do safety in one industry and want to understand how it's done in another. Similarly, you might be familiar with safety practices in one country but want to know how things are done elsewhere.
Topics: System Safety Assessment
In this series of posts, we take you through a suite of safety analysis tasks. They are designed to deal with a complex system, but can be simplified (known as ‘tailoring’). We start with Preliminary Hazard Identification and work through detailed analyses, each with a different point of view of the system.
Topics: Work Health and Safety
Australian Work Health & Safety law, or WHS, addresses both design and workplace, or occupational, safety. It imposes duties upon designers, manufacturers, and importers of plant, structures, and substances.
Not finding what you are looking for? Please head over to the Connect Page and tell us what you need.
Simon Di Nucci
https://www.safetyartisan.com/topics/
Here are the main topics taught by The Safety Artisan. Each page will take you to several teaching videos and other resources. Go to the Connect page to see how you can get updates every time a video or resource is added.
Start Here
Start here if you are new to safety! The posts featured on this page introduce basic safety topics, such as definitions and fundamental safety concepts. You can also start here if you know how to do safety in one industry and want to understand how it's done in another. Similarly, you might be familiar with safety practices in one country but want to know how things are done elsewhere.
Topics: System Safety Assessment
In this series of posts, we take you through a suite of safety analysis tasks. They are designed to deal with a complex system, but can be simplified (known as ‘tailoring’). We start with Preliminary Hazard Identification and work through detailed analyses, each with a different point of view of the system.
Topics: Work Health and Safety
Australian Work Health & Safety law, or WHS, addresses both design and workplace, or occupational, safety. It imposes duties upon designers, manufacturers, and importers of plant, structures, and substances.
Not finding what you are looking for? Please head over to the Connect Page and tell us what you need.
Simon Di Nucci
https://www.safetyartisan.com/topics/
Monday, August 26, 2024
Work Health and Safety
Australian Work Health & Safety law, or WHS, addresses both safe design and workplace (occupational) safety. It imposes duties upon designers, manufacturers, importers, and suppliers of plant, structures, and substances.
The four-lesson discount bundle, including Safe Design, is available here at a Discount!
WHS Law in Practice
WHS legislation is powerful and elegant, and it yields a lot of useful content, whether you are in an Australian jurisdiction or not. It is based on the UK’s approach to health and safety at work, but it has incorporated lessons learned from four decades of experience there.
In 2011, Safe Work Australia developed the model work health and safety (WHS) laws to be implemented across Australia. To become legally binding the Commonwealth, states and territories must separately implement them as their own laws. Safe Work Australia is responsible for maintaining the model WHS laws, but we don’t regulate or enforce them.Safe Work Australia
However, Australia’s federal system complicates the application of our laws. The Safety Artisan will attempt to cut through this complexity and explain the core concepts needed for practical success.
WHS Codes of Practice
Safe Work Australia notes that:
Model Codes of Practice are practical guides to achieving the standards of health and safety required under the model WHS Act and Regulations.Safe Work Australia
They also go on to say:
An approved code of practice applies to anyone who has a duty of care in the circumstances described in the code. In most cases, following an approved code of practice would achieve compliance with the health and safety duties in a jurisdiction’s WHS Act and Regulations.
Like regulations, codes of practice deal with particular issues and do not cover all hazards or risks that may arise. Health and safety duties require you to consider all risks associated with work, not only those risks that regulations and codes of practice exist for.
While approved codes of practice are not law, they are admissible in court proceedings. Courts may regard an approved code of practice as evidence of what is known about a hazard, risk or control and may rely on the relevant code to determine what is reasonably practicable in the circumstances.
We ignore these words at our peril!
Head back to the Topics Page for more safety training.
Simon Di Nucci
https://www.safetyartisan.com/work-health-and-safety/
Australian Work Health & Safety law, or WHS, addresses both safe design and workplace (occupational) safety. It imposes duties upon designers, manufacturers, importers, and suppliers of plant, structures, and substances.
The four-lesson discount bundle, including Safe Design, is available here at a Discount!
WHS Law in Practice
WHS legislation is powerful and elegant, and it yields a lot of useful content, whether you are in an Australian jurisdiction or not. It is based on the UK’s approach to health and safety at work, but it has incorporated lessons learned from four decades of experience there.
In 2011, Safe Work Australia developed the model work health and safety (WHS) laws to be implemented across Australia. To become legally binding the Commonwealth, states and territories must separately implement them as their own laws. Safe Work Australia is responsible for maintaining the model WHS laws, but we don’t regulate or enforce them.Safe Work Australia
However, Australia’s federal system complicates the application of our laws. The Safety Artisan will attempt to cut through this complexity and explain the core concepts needed for practical success.
WHS Codes of Practice
Safe Work Australia notes that:
Model Codes of Practice are practical guides to achieving the standards of health and safety required under the model WHS Act and Regulations.Safe Work Australia
They also go on to say:
An approved code of practice applies to anyone who has a duty of care in the circumstances described in the code. In most cases, following an approved code of practice would achieve compliance with the health and safety duties in a jurisdiction’s WHS Act and Regulations.
Like regulations, codes of practice deal with particular issues and do not cover all hazards or risks that may arise. Health and safety duties require you to consider all risks associated with work, not only those risks that regulations and codes of practice exist for.
While approved codes of practice are not law, they are admissible in court proceedings. Courts may regard an approved code of practice as evidence of what is known about a hazard, risk or control and may rely on the relevant code to determine what is reasonably practicable in the circumstances.
We ignore these words at our peril!
Head back to the Topics Page for more safety training.
Simon Di Nucci
https://www.safetyartisan.com/work-health-and-safety/
Monday, August 19, 2024
Home
The Safety Artisan gives you:
1. The flexibility that enables you to work and study2. Easy access to recorded classes to watch later3. Dynamic delivery based on practical experience
Learn safety engineering with me: a current industry professional with 25 years of experience.
Blog | Courses | Academy (Webinars+) | Email
The Safety Artisan: Latest Articles
Free Lessons
Preliminary Hazard Identification & Analysis Guide
System Safety Concepts & Principles
Risk Management 101
Safety Analysis Lessons
System Safety Assessment (Mil-Std-882E) Course
Foundations of System Safety Course
Hazard Identification Lesson
Software/Safety Lessons
Principles of Safe Software Course
Identify & Analyze Functional Hazards Course
My CISSP Exam Journey Lesson
Testimonials
The way you teach this subject makes it comprehensible and part of an integral whole. It seems like your approach is rare (and valuable) in the world of System Safety.Thomas AnthonyDirector, Aviation Safety and Security ProgramViterbi School of EngineeringUniversity of Southern California
Understanding safety law can be difficult and, at times, confronting. Thankfully, Simon has a knack of bringing clarity to complex legal requirements, using real work examples to help understanding. I highly recommend Simon to any director or manager wanting to understand their legal obligations and ensure a safe workplace.Jonathan Carroll, Senior Leadership, Pacific National
Valuable information, Clear explanations, Engaging delivery, Helpful practice activities, Accurate course description, Knowledgeable instructor.Manuel Louie B. Santos, reviewing “Risk Management 101”
Explanation about the military standard was very interesting, because for the first time somebody talked about possible disadvantages.Henri Van Buren, reviewing “System Safety Risk Analysis Programs”
4,500+ Students on Udemy
200+ Reviews, scoring:
- Principles of Software Safety Standards (4.48 out of 5.00);
- How to Design a System Safety Program (4.08 out of 5.00);
- How to Prepare for the CISSP Exam (4.61 out of 5.00); and
- Risk Management 101 (4.39 out of 5.00).
Why Safety Engineering Training?
The world needs safety engineers - a lot of them. Everything we use needs to be designed, manufactured, supplied, transported, and so on, and we need to do that without causing harm.
So, there’s a lot of need for safety engineering training. Want a (well-paid) career as a safety engineer? Need to do a safety-engineering-related task or project? Do you need to understand what your team is doing? Maybe you need to ask - or answer - the right questions in an interview.
There’s a lot of need for safety engineering skills, but they are difficult to get because training places are quite limited. Qualifications are expensive and take a long time to acquire.
I hope that by putting these lessons online, you’ll find them helpful. Who am I? Learn more.
It’s about Countering Fear – and Increasing Confidence
I decided to launch this site because I think there is a lot of fear around safety. People worry about getting it wrong, and therefore sometimes that can result in poor behaviors or poor performance. They shy away from doing anything about safety rather than just doing what they can.
This is a shame because safety is often just structured common sense.
It’s an engineering discipline like any other. Except that we need to involve people other than engineers. We need to involve operators, maintainers, and regulators. We need to involve end-users. So it’s quite a social activity as well, which I’m afraid can be a challenge for some of us engineers! (I’m as guilty of that as anybody else.) Nevertheless, there’s a lot we can do, and it isn’t as difficult as we think it is.
About the Author
learn more
Simon Di Nucci
https://www.safetyartisan.com/
The Safety Artisan gives you:
1. The flexibility that enables you to work and study2. Easy access to recorded classes to watch later3. Dynamic delivery based on practical experience
Learn safety engineering with me: a current industry professional with 25 years of experience.
Blog | Courses | Academy (Webinars+) | Email
The Safety Artisan: Latest Articles
Free Lessons
Preliminary Hazard Identification & Analysis Guide
System Safety Concepts & Principles
Risk Management 101
Safety Analysis Lessons
System Safety Assessment (Mil-Std-882E) Course
Foundations of System Safety Course
Hazard Identification Lesson
Software/Safety Lessons
Principles of Safe Software Course
Identify & Analyze Functional Hazards Course
My CISSP Exam Journey Lesson
Testimonials
The way you teach this subject makes it comprehensible and part of an integral whole. It seems like your approach is rare (and valuable) in the world of System Safety.Thomas AnthonyDirector, Aviation Safety and Security ProgramViterbi School of EngineeringUniversity of Southern California
Understanding safety law can be difficult and, at times, confronting. Thankfully, Simon has a knack of bringing clarity to complex legal requirements, using real work examples to help understanding. I highly recommend Simon to any director or manager wanting to understand their legal obligations and ensure a safe workplace.Jonathan Carroll, Senior Leadership, Pacific National
Valuable information, Clear explanations, Engaging delivery, Helpful practice activities, Accurate course description, Knowledgeable instructor.Manuel Louie B. Santos, reviewing “Risk Management 101”
Explanation about the military standard was very interesting, because for the first time somebody talked about possible disadvantages.Henri Van Buren, reviewing “System Safety Risk Analysis Programs”
4,500+ Students on Udemy
200+ Reviews, scoring:
- Principles of Software Safety Standards (4.48 out of 5.00);
- How to Design a System Safety Program (4.08 out of 5.00);
- How to Prepare for the CISSP Exam (4.61 out of 5.00); and
- Risk Management 101 (4.39 out of 5.00).
Why Safety Engineering Training?
The world needs safety engineers - a lot of them. Everything we use needs to be designed, manufactured, supplied, transported, and so on, and we need to do that without causing harm.
So, there’s a lot of need for safety engineering training. Want a (well-paid) career as a safety engineer? Need to do a safety-engineering-related task or project? Do you need to understand what your team is doing? Maybe you need to ask - or answer - the right questions in an interview.
There’s a lot of need for safety engineering skills, but they are difficult to get because training places are quite limited. Qualifications are expensive and take a long time to acquire.
I hope that by putting these lessons online, you’ll find them helpful. Who am I? Learn more.
It’s about Countering Fear – and Increasing Confidence
I decided to launch this site because I think there is a lot of fear around safety. People worry about getting it wrong, and therefore sometimes that can result in poor behaviors or poor performance. They shy away from doing anything about safety rather than just doing what they can.
This is a shame because safety is often just structured common sense.
It’s an engineering discipline like any other. Except that we need to involve people other than engineers. We need to involve operators, maintainers, and regulators. We need to involve end-users. So it’s quite a social activity as well, which I’m afraid can be a challenge for some of us engineers! (I’m as guilty of that as anybody else.) Nevertheless, there’s a lot we can do, and it isn’t as difficult as we think it is.
About the Author
learn more
Simon Di Nucci
https://www.safetyartisan.com/
Subscribe to:
Posts (Atom)
Australian vs. UK Safety Law This post, Australian vs. UK Safety Law compares the two approaches, based on my long experience of working on...
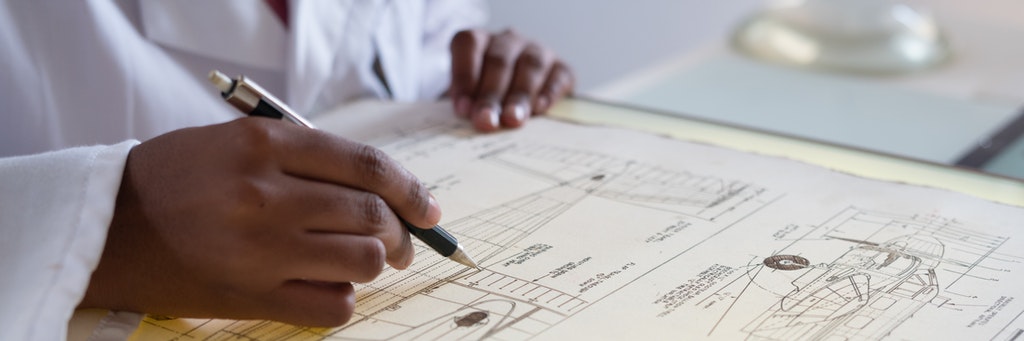
-
Introduction to System Safety Risk Assessment In this 'Introduction to System Safety Risk Assessment', we will pull together several...
-
How to Get the Most fromThe Safety Artisan #2 Hi everyone, and welcome to The Safety Artisan. I'm Simon, your host. This is 'How to...
-
Q&A: Reflections on a Career in Safety Now we move on to Q&A: 'Reflections on a Career in Safety'. Q&A Session | Q...