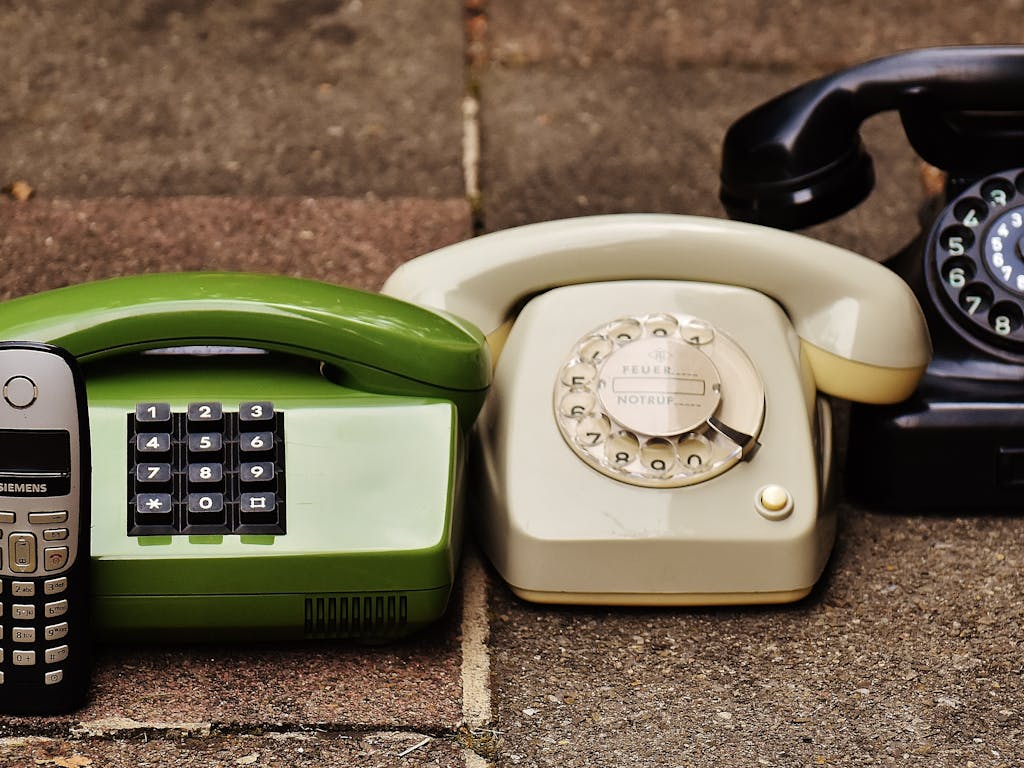
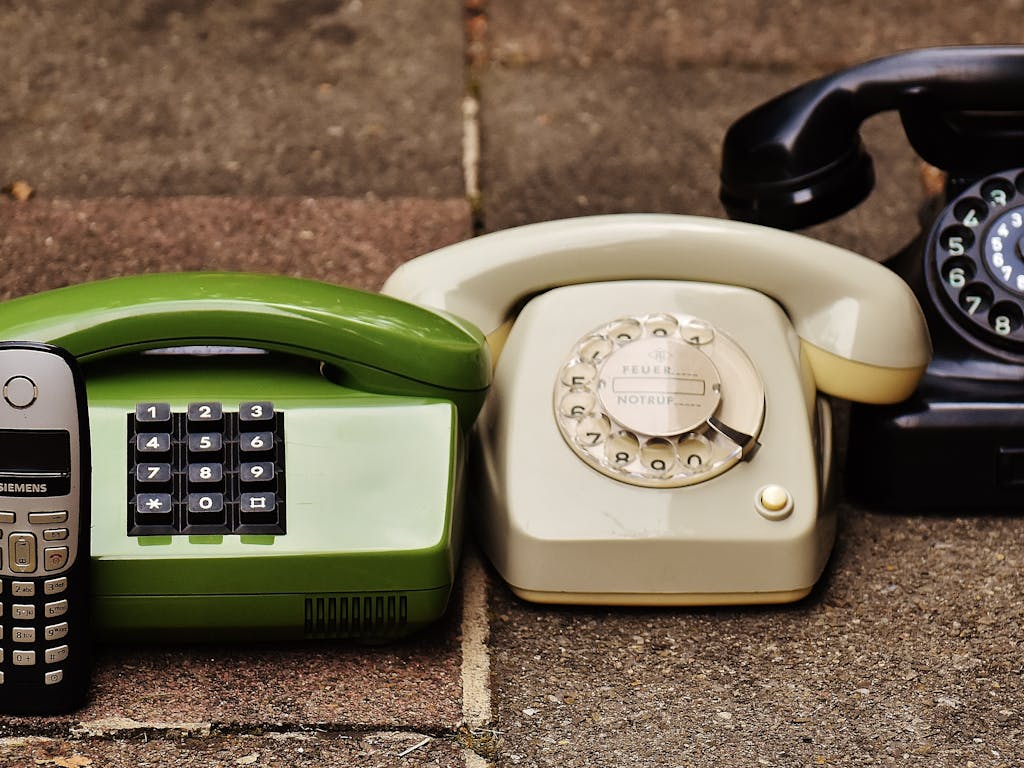
The Lifelong Evolution of a Safety Case
Introduction
In The Lifelong Evolution of a Safety Case, we look at how to Review and revise a Safety Case and Re-Issue a Safety Case Report.
When it comes to ensuring safety throughout any Product, System, or Service lifecycle, reviewing and revising the Safety Case isn’t just a recommendation—it’s essential. The age or status of equipment isn’t simply about how old it is. Instead, it reflects an understanding of its condition, the effects of changes, and its performance in varying environments over time. Let’s dive into the key principles of maintaining and revising a Safety Case and the potential risks and strategies to avoid them.
Why Review the Safety Case?
Changes in operations, equipment condition, or organizational controls can disrupt the assumptions on which the original Safety Case was built. Recognizing when a review is needed ensures safety remains uncompromised.
Here are examples of scenarios that demand attention:
- Structural Modifications: Repairs or upgrades impacting safety.
- New Activities: Introduction of new tasks or uses for the equipment.
- Environmental Changes: Shifts in operational environments or equipment roles.
- Incident Data: Insights from accidents or maintenance inspections.
- System Evolution: Decommissioning, extended use, or technological upgrades.
Figure: Relationship between the Safety Management System and Safety Case in terms of Age and Status
Relationship between the Safety Management System and Safety Case
Challenging Assumptions: The Foundation of Safety
A Safety Case is never static—it evolves as evidence and conditions change. It’s vital to challenge existing arguments continually. If new evidence undermines the validity of the Safety Case, steps like obtaining further proof, implementing corrective actions, or, in extreme cases, halting operations may be necessary.
Consider this: what was deemed safe at one time might become risky due to wear, updates, or new findings. Regular reviews ensure the Safety Case remains robust and relevant.
Ownership and Administration: Who's in Charge?
The custodian of the Safety Case is the Project Safety Manager, the linchpin in ensuring safety throughout the lifecycle of the system. This individual must coordinate all safety activities, maintain the Safety Case, and oversee its interaction with the Safety Management System (SMS).
While contractors may handle the technical details, the responsibility for ensuring the integrity and adequacy of the Safety Case rests with the appointed safety delegation holder.
Records Matter: Documenting Safety
Every decision, from hazard mitigation to safety strategy adjustments, must be meticulously recorded. Key documents feeding into this process include:
- System Requirements Document: Detailing specific safety needs.
- Customer-Supplier Agreement: Outlining deliverables.
- Through-Life Management Plan: Ensuring continuity in safety oversight.
A central part of this process is the Hazard Log, which serves as the repository of all identified risks and their management status. (see Procedure SMP11 – Hazard Log).
Avoiding Pitfalls: The Warnings
The warnings and project risks identified in all the other procedures, from SMP01 to SMP11 can manifest themselves through effects on the Safety Case, as it brings their outputs together. Also, there are other project risks specific to the Safety Case.
Neglecting regular reviews or documentation can lead to significant issues, including:
- Delays in Safety Approvals: Failure to engage approval authorities early can result in unmet safety requirements and service delays.
- Outdated Safety Cases: A mismatch between documentation and the system’s current state undermines credibility.
- Inadequate Risk Analysis: Improper techniques during safety assessments may yield an incomplete Safety Case.
- Lost Records: Poor documentation management can erode trust in the safety process.
Completing the Circle: The Role of Collaboration
Maintaining a credible and effective Safety Case is a collective effort. Contractors, safety committees, and stakeholders must work in concert to identify and mitigate hazards. Sharing data, especially during transitions between contractors, is crucial to avoiding gaps in safety oversight.
Wrapping Up
The Safety Case is more than a set of documents—it’s a dynamic framework ensuring that safety risks are continuously managed throughout the lifecycle of a system. With proper reviews, updates, and collaboration, it provides confidence that safety remains a top priority, no matter the changes a system undergoes.
This blog article is Part 3 of a series. It follows on from Part 2.
Meet the Author of 'The Lifelong Evolution of a Safety Case'
Learn safety engineering with me, an industry professional with 25 years of experience, I have:
•Worked on aircraft, ships, submarines, ATMS, trains, and software;
•Tiny programs to some of the biggest (Eurofighter, Future Submarine);
•In the UK and Australia, on US and European programs;
•Taught safety to hundreds of people in the classroom, and thousands online;
•Presented on safety topics at several international conferences.
#HazardLogBestPractices #LifecycleSafetyCaseReview #MaintainingSystemSafety #OperationalRiskManagement #ProjectSafetyManagerRole #RiskAssessmentLifecycle #SafetyCaseDocumentationTips #SafetyCaseManagement #SafetyManagementSystemIntegration #SafetyOversightinProjects
Simon Di Nucci https://www.safetyartisan.com/?p=4149
No comments:
Post a Comment