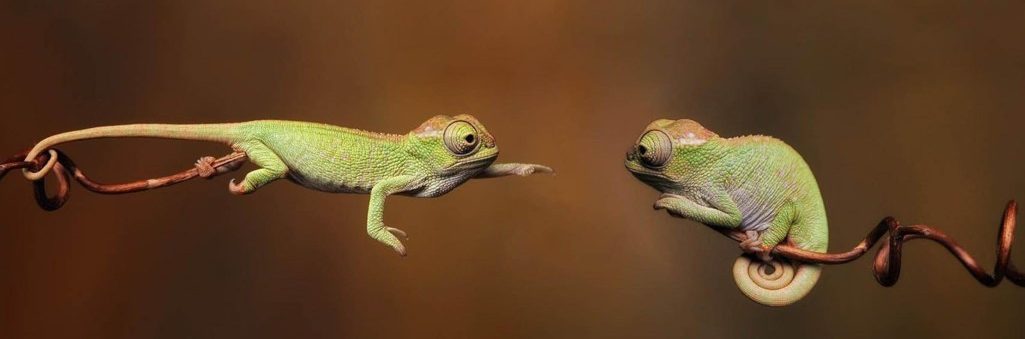
Q&A: Reflections on a Career in Safety
Now we move on to Q&A: 'Reflections on a Career in Safety'.
Q&A Session | Q&A Session | Q&A Session | Q&A Session
How do you Keep People Engaged with Safety?
Q. I was thinking of an idea as I was walking here, and you did mention just in your slide about going with the flow that sometimes people who stop listening to you I've seen a lot of people come up with safety systems where there's a lot of forms and paperwork to fill out. And a lot of the people who are doing it just go. It's just paperwork. It doesn't do anything for safety. It's somebody else covering their butt.
Whereas what when I look at them, what they are is almost a prompt to get people to think about the things that can bite them. Yeah. Keep that idea of what's in front of them in their heads rather than letting that go into the. Is just paperwork for paperwork’s sake. Yeah. How do you keep them engaged in using that as a tool rather than a liability reduction?
A. Yeah, I think, first of all, there's got to be a bit of education. They've got to understand that they're dealing with things that are potentially dangerous. I mean, that's required anyway. You've got to warn users and them the information that they need. But I think mostly it's about how you engage with people. If you show if you sell it to them, there's a benefit to doing this. And you talk in a language that they understand you're much more likely to get listened to.
I've been to lots of places where people have had awful procedures that don't help them get the job done, it's slow and clunky and they often get ignored. So the trick is to try and make the procedures as helpful to get the job done as possible. And of course, if you can build in safety so people don't have to follow so many procedures, that's even better. If they physically can't do something dangerous, then that's great.
That's much more effective than procedures anyway. But it is all about speaking the user's language. So, I learned that with pilots, pilots have got a particular way of thinking and you can give them a rule that says don't do this, but it might not actually make any sense in that context. So you've got to understand what their context is. You can they can only follow a rule if it's based on information that's actually available to them.
So you can say, don't go below 10,000 feet while doing this or don't exceed the speed. Otherwise, the wings might fall off. That that they understand. If you gave them a load of technical garble about stuff, they probably wouldn't pay much attention.
That said, you do sometimes have to tell people the bleeding obvious because I remember a known British pilot took off in a plane where the fuel warnings were showing on the wing tanks, but the pilot still took the plane and then got in the air and no fuel was coming out of the wing. So he had to land the plane pretty quickly before it ran out of fuel. And I was going to bring in some advice to our pilots to say: don't do that. If you see the yellow stripes on the wings, that's a bad scene on the display. That's a bad sign. And somebody said to me, oh, no British pilot would be stupid enough to do that. And like a fool, I believed him.
So they did do that. And then right now we're having the rule that says, don't do that, because it was needed. So there's always a fine balance is a bit of give and take. Thanks for the questions. Yeah. Anyone else, anyone else?
Which Project was Most Influential on Your Life?
Q. If you can share what's one of the projects that you worked on that was probably the most influential in your life or that you thought was definitely helpful for where you are now.
A. That’s a really good question. Well, I suppose the big one in my life was Eurofighter because I spent 13 years, on and off, on Eurofighter and I got to work with some fantastic people; in theory, I was their manager. But in reality, they knew 100 times as much about the subject as I did and I learned a lot from them.
So, yeah, I would say because of that, the sheer number of people. But there were lots of jobs where I got a lot out of it professionally or personally … But yeah, I think it's the people, wherever you are.
I've seen a lot of teams. They've got terrible workplace conditions, work in an old dilapidated building. They haven't got enough spares. They haven't got enough tools or anything. Everything is against them. But if they're a good bunch of people, they'll still achieve great things and enjoy doing it.
How do you Make a Safety System Responsive?
Q. OK. Oh, so you're talking about these very complicated systems where you permitted people to do work so really planned because they're so difficult. You've really planned how work has to happen. But the things that you're working on, stuff that theoretically most operations at the moment are small arms and things, but people can shoot holes in the things that you're working on. And if the 10,000 tanks come over, then you've got potentially a lot more holes all of a sudden.
How do you go from that very regimented system and then work out how to make it also really, really fast and responsive to something that keeps throwing up problems at a much higher rate than I'd imagine you can fill out the forms to give permission to the person to do the work as is the usual practice.
A. So you're using the same system over and over and over again. And people will spend years using the same system, maybe on the same equipment or the same plane or whatever it is.
So people are well-practiced. Another technique is if people are overtrained and they got lots of experience, then they can often cope in adverse circumstances. So sometimes you just have to cut corners in order to get a job done. And it's having the experience and the knowledge to do that safely and still get the result you need that, that's the judgment side. That's the stuff that you can't write down. But mostly it's through practice.
So, we would follow a very regimented process. But once you've done it enough times, it became second nature. It's like training an athlete. Once you've got the regular way of doing things down pat, it then becomes a lot easier to spot when you've got to do something a bit different and cope with it.
Q&A: How do you Determine Safety Requirements? How do you Detect Safety Issues in Software?
Q. So I'll try and combine these because the time's getting on and I've got a lot of questions, you're talking about safety and software and safety being an emergent phenomenon, and you're not necessarily going to know that something you do in software is going to cause. An issue with the typhoon is very software-controlled aircraft, so the computer says is close to what's going to happen over the pilot in a lot of ways. You also talked about putting safety into requirements.
Some requirements may or may not like you could have a direct safety requirement, but there could be other requirements that can impact safety without it being explicit. Yeah, how do you detect that in a set of system or user requirements? And how do you detect safety issues in software systems that look like they're doing what they're supposed to do?
A. Yeah, so do the requirements bit first. Sometimes you get a bunch of requirements and you've just got to go through them and look for safety implications. Sometimes it's really obvious like the customer says, I want this safety system installed in my ship. The ship has got to be built in accordance with certain rules, class rules, or whatever they might be. And you go, OK, a lot of that will be safety-related.
And sometimes you've got to do some work. You've got to decompose the requirements and look at how are you going to solve the problem and go, OK, the requirements are pushing us to have this high-energy system in my ship. OK, there are safety issues with managing that and making sure it doesn't get out of control. So sometimes it only emerges after you've done further work after you've kind of decomposed your initial requirements.
But if the people doing the requirements, you might have systems engineers on the client-side and on the provider side. If they're doing their job well, they’re processing the requirements. And these things will tend to emerge quite well. If you've got good systems engineering. So that's that one.
The software one, it all depends on how safe or how dependable you want the software to be. Ultimately, the Eurofighter had a software-controlled flight control computer, and the aircraft in certain aspects was unstable. So the pilot could not fly it without the computer. So that's as tough as it gets in terms of software safety, the computer cannot fail. OK, and to achieve that level of safety, the state of the art at the time was going through the source code in forensic detail, nailing down the compiler so that it was only allowed to do very basic things.
And then you produce the object code and then you go through the object code in forensic detail and then test it to death. So lots and lots of processes applied and there were still errors in the software because there always will be because there are so many. But you can at least say none of these errors will result in an unsafe outcome, provided, of course, that you've got a sufficiently detailed specification to say this is safe and this is not OK.
So if you're if you've got to go to that level of detail, you can forensically go through things. And then there are if you've heard of Safety Integrity Levels (SILs) or safety integrity requirements for different cells or different says, you can have a cookbook approach where you use different techniques. Usually, the toughest SIL is the state of the art at the time that the standard was created. That's very crudely how you do it, and hopefully, you've got some competent people as well.
Host: Thank you. Thank you so much for sharing your time with us and explaining your journey through safety. Something that I think was interesting is that you raised it here.
How do you Deal with People Using Stuff in Ways it Wasn't Designed for?
Q. I understand people's motivation, the context of people's motivations for using the equipment. And people might use it in ways that you don't even dream of. Right, you might have designed something to do this or something. And then people stand on it to reach something else, that kind of thing, isn't it? I think when you move from being at university and going into industry and seeing how the equipment is actually used, you can blow your mind sometimes. Yeah.
A. Yeah. Even people who had worked in the Ministry of Defence , my boss was horrified at the idea that the Air Force would fly a plane that wasn't totally serviceable. And to me, that was completely routine. None of them worked totally as intended. There were some features that we just disabled all the time.
Host. So, yes, that is also something that blows your mind. Oh, thank you very much, Simon. Thank you and thank you, kind audience. Thanks for your participation.
Q&A Session | Q&A Session | Q&A Session | Q&A Session
This was part of a lecture to the University of Adelaide SEIP Course. You can the other sessions, as follows:
- Part 1 https://www.safetyartisan.com/2021/06/30/reflections-on-a-career-in-safety-part-1/
- Part 2 https://www.safetyartisan.com/2021/07/07/reflections-on-a-career-in-safety-part-2/
- Part 3 https://www.safetyartisan.com/2021/07/14/reflections-on-a-career-in-safety-part-3/
- Part 4 https://www.safetyartisan.com/2021/07/21/reflections-on-a-career-in-safety-part-4/
- Part 5 https://www.safetyartisan.com/2021/07/28/reflections-on-a-career-in-safety-part-5/
So that was 'Reflections on a Career in Safety: Q&A'. Did you find it useful?
#howdoyoumakeasafetysystemresponsive #howtodeterminesafetyrequirements #issafetyagoodcareer #Q&A #questionsandanswers #whichprojectwasmostinfluentialinyourlife #whychoosesafetycareer
Simon Di Nucci
https://www.safetyartisan.com/2021/08/04/reflections-on-a-career-in-safety-qa/